Металлурги взялись за мастерок
17.09.2007Последние десять лет в России строились только холдинги. И вот теперь строятся заводы. И речь идет не только о техническом перевооружении или достройке новых цехов — инвесторы готовы возводить заводы с нуля. Из более десяти green-field-проектов, ведущихся сейчас в России, есть два даже по мировым меркам крупных и фактически завершенных. Это Хакасский алюминиевый звод (ХАЗ), построенный «Русалом», и литейно-прокатный комплекс «ОМК-Сталь» (ЛПК), возведенный Объединенной металлургической компанией.
Мы решили съездить на эти предприятия, чтобы своими глазами увидеть новую российскую металлургию. Оба завода почти готовы. На ХАЗе работают три очереди, последняя будет введена осенью этого года. В январе 2008−го планируют начать выплавлять сталь и делать прокат на ЛПК. Мы спешили попасть туда, пока с площадок не уехали рабочие. Уж очень хотелось взглянуть не только на сами заводы, но и на то, как их строят. Как никак, такого в стране уже не было очень давно, последние крупные промышленные предприятия возводились более двадцати лет назад, еще во времена СССР.
Давно уже нет СССР. Забылись и навыки централизованного планирования, и страсть к гигантским масштабам. Тогда откуда истоки этой строительной прыти? Неужели что-то осталось от советского опыта индустриального строительства? Ведь теперь все проблемы, связанные с ним, приходится решать частному капиталу. Есть ли преемственность поколений инвесторов и строителей и как частные инвесторы организуют крупное промышленное строительство? Чтобы понять все это, мы и отправились в Выксу и Саяногорск.
Наследие братьев Баташевых
Выкса — небольшой город в Нижегородской области с богатым металлургическим прошлым. Это прошлое бьет в глаза: улицы пестрят плакатами «Выксунскому металлургическому заводу 250 лет».
Юбилейная дата интригует. Выясняется, что первыми заводчиками в этих местах были братья Баташевы. Выходцы из семьи тульских кузнецов, переквалифицировавшихся в промышленников, они сформировали новыйметаллургический центр в центральных губерниях, построив более десяти заводов. Выксунский завод они основали в 1757 году. После смерти братьев, уже в первой четверти XIX века, ВМЗ неоднократно менял владельцев, к концу века им управляли немцы, потом предприятие было национализировано. В советские времена на базе ВМЗ был создан один из крупнейших в СССР трубных заводов. Новейший период его истории связан с Объединенной металлургической компанией (ОМК). ВМЗ вошел в ее состав в 1999 году, был модернизирован. Потом появились планы создать вокруг трубного производства новыйметаллургический комплекс, который являл бы собой завершенную производственную цепочку от плавильной печи до готовой трубы. Баташевых в ОМК вспоминают часто, перед офисом ВМЗ им даже поставили бронзовый памятник. Получается, что нынешний владелец ВМЗ продолжает многовековые традиции. Вроде бы не безликая индустрия, а дело со своей историей.
А ведь советская индустриализация полностью искоренила подобный формат ведения дел в тяжелой промышленности. Его элементы сегодня можно найти, пожалуй, лишь среди небольших предприятий малого и среднего бизнеса. Тем удивительнее было обнаружить возрождение этих традиций в крупной металлургической компании.
Литейно-прокатный цех «ОМК-Стали», ради которого мы и приехали в Выксу, строится в первую очередь ради ВМЗ. Сейчас у завода нет собственного сырья — стального листа. Строящийся ЛПК может полностью закрыть потребность Выксунского металлургического в листе для труб малого и среднего диаметра (21–530 мм). Первая очередь ЛПК рассчитана на 1,5 млн тонн стали. Потребности ОМК составляют порядка 0,8 млн тонн стального листа, но к моменту запуска первой очереди ЛПК потребности входящих в ОМК Выксунского и Альметьевского трубных заводов достигунт примерно миллиона тонн. К 2010−му они должны увеличиться до 1,3 млн тонн стального листа.
Время — деньги. Большие
Наш приезд в Выксу совпал с подготовкой к празднованию Дня металлурга и юбилея завода. Офис лихорадило: вверх и вниз по лестницам сновали люди, звонили телефоны. В суматохе мы разыскали исполнительного директора «ОМК-Стали» Константина Питюла. Одет неформально, вместо костюма джинсы и рубашка. В костюме по стройплощадке не особо походишь, а он почти все время проводит там. Кстати, это не первый его подобный опыт. Питюлу доводилось руководить строительством как минимум шести крупных металлургических заводов, и впоследствии он на некоторое время оставался там на посту директора. Пожалуй, в России сейчас найдется немного управленцев с подобным опытом.
Пока мы ждем машину, чтобы ехать на ЛПК, интересуюсь, сильно ли отличаются советские стройки от нынешних. Константин Питюл отвечает, что везде свои преимущества, но все-таки с планированием в СССР было лучше: удобная система комплектации, централизация поставок материалов и оборудования. Звонит мобильный, мой собеседник уходит, через некоторое время возвращается: «Вот, например, как раз одно российское машиностроительное предприятие задерживает поставки оборудования». Это не самый редкий рабочий момент. Удивительно, как при этом строители умудряются не выбиваться из графика, тем более что ЛПК вот уже два года строится без финального варианта проекта. Последние бумаги приходят от проектировщиков только сейчас. Это пример так называемого параллельного строительства и проектирования. В советские времена за такие фокусы сажали, но сейчас, похоже, допустимо все — лишь бы строили. «В принципе это необычно, — поясняет Константин Питюл, — потому что в таком случае инвестор подвергается большим рискам — стоимость проекта может возрасти в три-четыре раза. Известны такие примеры».
Два года назад представители ОМК рассчитали, что на первую очередь завода (всего их две) мощностью 1,2 млн тонн стали в год им потребуется 600 млн долларов. Однако по ходу проекта изменились и мощностные, и стоимостные параметры. Использование аналогичного сталеплавильного оборудования на китайских предприятиях показало, что оно может изготавливать до полутора миллионов тонн стали и более. Это приятное открытие. Неприятным оказалось то, что, как это всегда и бывает, смета строительства возросла более чем на 200 млн долларов. Правда, это уже с построенными элементами второй очереди. В результате общие мощности должны достичь 2,5–3 млн тонн горячего проката в год, и обойдутся они примерно в 1,5 млрд долларов, точные цифры в компании назвать не в состоянии.
ОМК пошла на миллиардные траты вполне осознанно, компания остро нуждается в собственном сырье для производства труб. Благодаря ряду технологических решений литейно-прокатный комплекс должен стать более экономичным металлургическим предприятием, чем большинство заводов в отрасли, то есть себестоимость производства листа будет ниже, чем цена покупаемого на стороне проката. Кроме того, производя лист самостоятельно, ОМК сможет делать металл с особыми свойствами. «Требования к потребительским свойствами труб меняются, и чтобы отвечать запросам рынка, ОМК должна предлагать ему новые виды труб, — рассказывает Константин Питюл, пока мы едем на завод. — Большой металлург, у которого мы покупаем лист сейчас, еще подумает, что ему выгоднее — разрабатывать металл со специальными свойствами или выпускать продукцию для массового сегмента рынка».
Разговор на турецко-нижегородском
Подъезжаем к площадке. Перед нами вырастают ангароподобные сооружения. Некоторые уже достроены, но на большинство металлоконструкций «мясо» пока не надето. Среди этих индустриальных скелетов месят глину грузовики. «У нас почти все готово: корпуса достроены, оборудование смонтировано», — показывает Константин Питюл. Но на первый поверхностный взгляд все это выглядит довольно разрозненно. Массивы корпусов настолько подавляют, что рабочих практически не видно, хотя нам рассказали, что на стройке работает больше трех с половиной тысяч человек, две тысячи из них — турецкие строители. Мой собеседник поясняет, что генеральный подрядчик — турецкая строительная компания GamaIndustrial. Компания более тридцати лет строит подобные промышленные объекты по всему миру. Отношения с субподрядчиками ведет она, она же набирает рабочих.
Почему же турки, где же советская школа массового промышленного строительства? Делаю предположение, что услуги турецкой компании обошлись дешевле. Константин Питюл объясняет, что проблема вдругом — конкуренции с российскими подрядчиками вообще не получилось, так как «в России сейчас нет опытных мощных компаний, которые занимались бы строительством таких комплексов. Я имею в виду не по частям, как делается на некоторых предприятиях, а сразу целиком». Кадры, рабочие — это самое уязвимое место в промышленном строительстве: «У нас остались лишь какие-то элементы, например, электро— и механомонтажные группы в России сильные, но строителей нет». Это следствие того, что больше двадцати лет подобных объектов в России не строили. Получается, что привлечение иностранных подрядчиков — непатриотичный, но вынужденный ход.
Доверить проект неопытной компании ОМК, видимо, не захотела. И из-за сложных условий строительства — без полной проектной документации. Ее, кстати, разрабатывали на Украине. Укргипромез — ныне независимая проектная организация, которая когда-то была филиалом главного московского Государственного института проектирования металлургических заводов (Гипромез). Ситуация с проектными институтами чуть лучше, чем с подрядчиками. Филиалы старого Гипромеза сейчас начинают возрождаться, но два года назад, когда ОМК искала разработчиков для ЛПК, выбора почти не было. «Мы рассматривали три варианта: либо московский Гипромез, либо украинский, либо магнитогорский. Магнитогорский отказался ввиду своей загруженности. Московский через год после подписания контракта с нами развалился, — вспоминает Константин Питюл. — Кадры сумел сохранить Укргипромез. Сейчас в нем работает больше тысячи человек, много молодежи». Сегодня этой тысячи уже недостаточно, так как фактически они делают большинство проектов и в России, и на Украине.
Улыбчивые рабочие охотно позируют нашему фотографу на фоне смонтированного прокатного стана. Удивляюсь, как им удается находить общий язык. На производственной площадке все вопросы решает турецкаяGama, но проблемы возникают и за пределами стройки на чисто человеческом уровне. Две тысячи рабочих живут в отдельном поселке уже два года, конечно, выходят в город, ухаживают за местными барышнями. Трое даже женились. Местным парням конкуренция не по душе, периодически вспыхивают конфликты вплоть до массовых драк. Рабочий, так сказать, момент.
Учимся экономить
Заходим в будущий литейный цех. Все устроено довольно компактно. Для России такой формат предприятия необычен. В черной металлургии остались либо небольшие предприятия мощностью до миллиона тонн, либо советские сверхгиганты производительностью от 4 до 12 и более миллионов тонн стального проката в год. Гиганты впечатляют, но такими махинами сложнее управлять, нежели небольшими заводами. В мире наибольшей популярностью сейчас пользуются так называемые мини-миллы — заводы мощностью до миллиона тонн стали в год. Они более экологичные, работают на металлоломе. Хотя по мировым меркам «ОМК-Сталь» — производство очень крупное, по типу организации, технологиям оно тяготеет именно к формату мини-милла.
На ЛПК технология предусматривает три вида использования сырья. В первом случае в печь будут закладывать только металлолом. Во втором — 80% металлолома и 20% чугуна. В третьем — около 45% металлолома, а все остальное — чугун и горячебрикетированное железо. Последний вариант будут использовать в случае, если понадобится получить наиболее чистый металл с высокими качественными характеристиками. Каких-то дополнительных манипуляций с перенастройкой печи не требуется. Еще пару лет назад свыше половины всего собранного в России лома шло на экспорт, сегодня большая часть остается в России. ЛПК не единственный претендент на лом как на дешевое сырье. Аналитики заговорили о дефиците. Поэтому, чтобы застраховать себя от перебоев с поставками и опять-таки не зависеть от внешних поставщиков, ОМКучредила собственную компанию для сбора металлолома.
По мощностям ЛПК к мини-заводу отнести нельзя, но «если под мини-миллом понимать производство с минимальным количеством операций от сырья до готовой продукции, то ЛПК — настоящий мини-милл», говорит Константин Питюл, демонстрируя путь, который будет проходить сырье для превращения в металлический лист: «Весь цикл займет всего два с половиной часа, и мы получим готовую продукцию». Технологические решения, которые выбрали на «ОМК-Стали», для России уникальны. Литейно-прокатное оборудование итальянской компании Danieli позволяет делать очень тонкую металлическую заготовку (сляб). Ее толщина 90–110 мм, это в два-три раза тоньше, чем на других российских металлургических предприятиях. Поскольку сляб выходит более тонким, требуется меньше операций для того, чтобы раскатать его до нужной формы на прокатном стане.
Урезанный цикл более экономичен. Во-первых, сокращаются энергозатраты. Во-вторых, на производстве требуется меньше рабочих и операторов. «У нас на всем производстве будет работать 850–900 человек, а, например, на ММК только обслуживанием одного прокатного стана занимается две тысячи человек», — объясняет Константин Питюл. Мы узнали, что эти 900 человек не придется искать на стороне. На новый заводперейдут рабочие, высвободившиеся после модернизации ВМЗ.
Конец прокатного стана теряется где-то вдали. Он тянется на 800 метров, вместе с корпусом литья получается здание длиной в километр. Весь комплекс занимает территорию 150 гектаров, или полтора квадратных километра. Площадь ЛПК в 17 раз меньше площади Новолипецкого меткомбината и почти в 80 раз меньше площади Магнитки. Последняя, правда, по этому параметру достойна Книги рекордов Гиннесса.
Понятно, что таких индустриальных феноменов, как Новолип или Магнитка, строить больше не будут. Это даже хорошо. Будущее как раз за компактными комплексами, подобными тому, что построила ОМК. Спрос на них будет только увеличиваться, вопрос лишь в том, когда в России появится рынок строительных услуг, рынок генподрядчиков, которые смогут этот спрос удовлетворить. Ведь те десять, а может, и больше новыхзаводов, уже пригрезившихся промышленным инвесторам, должны быть кем-то построены. Одним турецким генподрядчиком эту потребность не закрыть, а альтернатив пока не видно.(…)
Источник: журнал «Эксперт»
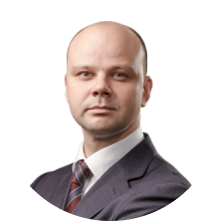