В промышленности растут большие данные
21.01.2019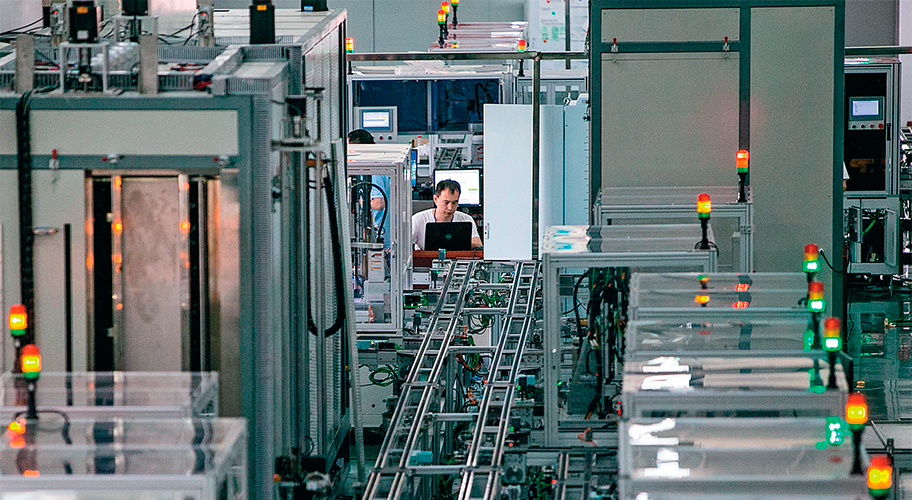
В области использования больших данных назревает перелом, который приведет к резкому изменению технологического уклада. Big Data уже нашли утилитарное применение в промышленности, но пока внедрение этих технологий в России сдерживается устаревшим оборудованием, с которого трудно получать информацию, и неготовностью инфраструктуры «читать» и анализировать данные.
«Передовиками» в использовании больших данных были разработчики поисковых систем, которые с помощью математического моделирования научились превращать поисковые запросы в реальные деньги. Возможно, теперь пришло время и промышленным предприятиям последовать их примеру. Тем более что в этой области у нас есть все шансы не отстать от западных стран.
В концепции «Индустрии 4.0» и в целом цифровизации производства именно Big Data становятся основой для принятия решений об изменениях процессов. Большими данными называют объемы информации, которые невозможно обработать традиционными способами, то есть с помощью обычного компьютера и в короткие сроки. Для работы с ними требуется специальное программное обеспечение и инфраструктура - центры обработки данных.
Впрочем, в России этот термин трактуется очень широко и, скорее, он похож на маркетинговый. Как отмечает Данила Целиканов, главный специалист по инновациям ПАО ММК, Big Data называют все, что связано с данными и математическими алгоритмами их обработки. В то время как классическое понимание термина предполагает наличие определенного объема информации - речь идет об огромных массивах данных, которых у большинства промышленных предприятий сегодня просто нет. «У нас нет больших данных в классическом понимании, - говорит Данила Целиканов. - Да, мы используем математические модели, строим их на неких массивах данных, накопившихся лет за десять. Но их нельзя назвать большими данными. Big Data у нас появятся, когда мы развернем проект в области интернета вещей, когда будут установлены тысячи полевых датчиков, с которых будут собираться терабайты информации».
По мнению Данилы Целиканова, оперировать большими данными могут ритейлеры с тысячами торговых точек и десятками тысяч наименований товара, сотовые операторы или энергетики с несколькими тысячами подстанций, с которых собирается цифровая информация. «Сейчас мы собираем данные, но, условно говоря, нам хватает сервера для их хранения и достаточно среды программирования R, чтобы их обработать, - говорит г-н Целиканов. - Это ничтожный объем по сравнению с цифровыми гигантами. Зато мы уже вовсю занимаемся матмоделированием и цифровыми двойниками».
Однако дело идет к тому, что к этому понятию - Big Data - металлурги вернутся буквально через три-пять лет, считает Данила Целиканов. Уже сейчас развиваются проекты в области интернета вещей, в этом году Магнитогорский металлургический комбинат, скорее всего, начнет тестировать сенсоры, которые будут размещаться на оборудовании. Если сейчас удается с помощью датчиков снимать информацию о полутора-двух процентах технологического процесса, говорит г-н Целиканов, то при развитии сенсоров и датчиков, возможностей использования локальных нейрочипов объем данных начнет быстро расти.
Если говорить о Big Data не в академически строгом понимании, то у российского бизнеса, как утверждает Дмитрий Карагулян, руководитель лаборатории по работе с большими данными (Big Data Lab) Фонда развития интернет-инициатив, в последние два года заметно растет интерес к сбору и анализу данных в «цифре». В течение первого года активно накапливалась экспертиза, а сегодня уже есть успешный опыт применения таких технологий, появилась возможность на основе работы с большими данными создавать продуктовые решения, применимые на производстве.
Как отмечают в 2050.Digital (разработчик решений для цифровизации), компании начинают понимать потенциальную ценность больших данных и рассматривать в том числе и «сырые» данные как полезный актив, даже если они не могут воспользоваться этой информацией прямо сейчас - построить предиктивные (предсказательные) модели или системы реагирования, работающие в режиме реального времени. Условия для работы с данными есть везде, где выстроен «нижний уровень» - система снятия параметров с оборудования и их регистрации. «На основании этих данных можно строить бесконечное количество моделей, но полезны будут только те, которые помогут решить конкретную проблему в бизнесе», - говорит Дмитрий Карагулян. Речь идет об аналитике, направленной либо на предиктивный анализ, либо на построение оптимальных бизнес-процессов.
Big Data существуют в тесной связке с интернетом вещей - вместе они позволяют производителям повысить связанность всех узлов производственной цепочки и бизнес-процессов в целом: например, научиться предсказывать необходимый состав сырья и колебания спроса и тут же перенастраивать производственные линии. Каким может быть эффект? Даже традиционный металлургический бизнес может изменить свое лицо: например, по-новому организовать сбыт и стать более ориентированным на розницу.
По мнению аналитиков аудиторско-консалтинговой компании КПМГ, сбором больших данных озаботились участники практически всех отраслей, хотя внедрение Big Data и происходит неравномерно. Если взять нефтяную отрасль, то здесь Big Data уже активно используются в геологоразведке и добыче, а вот переработка только начинает собирать данные.
По информации Алексея Зенкевича, руководителя подразделения «Промышленная автоматизация» компании Honeywell в России и странах Таможенного союза, одна из самых популярных областей применения больших данных в промышленности - мониторинг состояния оборудования. Анализируя информацию от датчиков, можно выявлять даже небольшие отклонения от нормального режима работы, быстро устранять причины снижения производительности и предотвращать вероятные поломки. С помощью предсказательной аналитики можно уйти от традиционной системы планово-предупредительных ремонтов, сокращать аварийные остановки и простои.
Дело в том, что с современных станков с числовым управлением можно «снять» большое количество данных, они снабжены десятками датчиков (реагирующих на температуру, вибрации, отслеживающих координаты деталей и т. д.). Как рассказывает Николай Петрухин, заместитель гендиректора ОАО «СТАН-сервис», современный комплекс датчиков в совокупности с системой обработки массивов информации позволяет отслеживать техническое состояние узлов и систем, заранее предупреждать пользователя об износах, необходимости проведения сервисных мероприятий. «Наибольший эффект от использования «умного» числового оборудования проявляется в случае объединения станочного парка участков, цехов, предприятий в единую сеть и их интеграции в глобальную ЕRP-систему предприятия. Объем анализируемых данных в этом случае возрастает в тысячи раз, и оптимизация работы оборудования, сокращение простоев, исключение брака позволяют кратно поднять производительность и уменьшить себестоимость продукции», - объясняет г-н Петрухин.
«Интерес к предиктивному анализу растет, - говорит Денис Касимов, гендиректор разработчика таких систем Clover Group (разработал систему «Умный локомотив» для группы компаний «Локотех»). - Но если говорить именно о тяжелой технике, то на рынке не много решений, готовых к внедрению».
Что касается оценок реального экономического эффекта от применения технологий мониторинга работоспособности оборудования, то, по словам Алексея Зенкевича, они помогают сократить на 10–15% время дорогостоящих простоев производства и снизить на пять процентов эксплуатационные затраты. Проекты, связанные с анализом данных об эффективности производственных процессов, окупаются за шесть-девять месяцев.
В этой области есть примеры. На Выксунском металлургическом заводе (входит в ОМК) автоматизировали планирование и управление ремонтными работами, чтобы сократить простои оборудования. В рамках проекта оборудование завода было снабжено NFC-метками на основе технологии идентификации путем беспроводной передачи данных. В компании говорят, что за первое полугодие работы системы они стали собирать почти в два с половиной раза больше данных о неисправностях оборудования, что позволило более адресно и своевременно проводить корректирующие мероприятия, чтобы не допускать внеплановых простоев. В то же время на 50% снизилось количество сообщений в системе о простоях оборудования и на 25% сократилась трудоемкость выполнения ремонтных работ.
Активно развивают проекты цифровизации Трансмашхолдинг и компания «Локотех», крупнейшая в России сервисная группа по обслуживанию и ремонту локомотивов. Программа цифровой трансформации включает в себя десятки различных инициатив, пилотные проекты уже запущены на Новочеркасском электровозостроительном заводе и в сервисном локомотивном депо (СЛД) Братское в Иркутской области.
«Цифровизация в депо Братское позволит нам правильно определить пути оптимизации технологических процессов и в целом повышения эффективности ремонтного производства посредством, например, изменения внутренних логистических потоков, расстановки персонала, уточнения последовательности выполнения ремонтных операций, оптимизации загрузки станков и оборудования, - рассказывает Игорь Бевзюк, гендиректор компании 2050.Digital, одного из участников проекта. - Сегодня внутри действующего депо отрабатывается порядка 200 цифровых решений, начиная с очков виртуальной реальности и заканчивая RFID-метками, которые используются во внутренней логистике и системах доступа». По словам Игоря Бевзюка, внедрение интеллектуальной системы «Цифровое депо» в СЛД Братское позволит повысить коэффициент технической готовности (КТГ) парка локомотивов на четыре процента, снизить операционные затраты на сервисное обслуживание на пять процентов, а неэксплуатируемый парк - на 25%.
Большие данные применяются и в целях прогнозирования спроса. Такую задачу ставит перед собой компания «Газпромнефть - смазочные материалы», которая в рамках внутреннего подразделения по machine learning (машинному обучению) разрабатывает систему анализа данных. Храниться и обрабатываться эти данные будут на платформе с открытым кодом доступа - open source, а значит, проблем не возникнет даже в случае санкционных ограничений. К разработкам впоследствии будут привлекать и крупных участников отрасли Big Data. Имея ассортимент продукции из 1500 позиций и 200 контрагентов в 76 странах, компания с помощью традиционных статистических инструментов не всегда могла четко прогнозировать спрос даже на месяц вперед. «В машинном обучении тоже заложен такой статистический механизм, но при этом система сама обучается каждый раз уточнять прогнозы и выявлять новые зависимости. В результате она может предугадывать то, что неподвластно жесткому алгоритму, который закладывается на базе формул по статистике», - объясняет Михаил Низкий, заместитель генерального директора по экономике и финансам компании «Газпромнефть - смазочные материалы». В этом году компания должна завершить сбор данных о продажах от контрагентов, аккумулировать их в большие данные, а в 2020 году планируется запустить проект по прогнозированию спроса.
Небольшая облачность
Но в целом цифровизация на производствах пока остается в зоне экспериментов. «Процентов на семьдесят технологии искусственного интеллекта состоят из опытно-конструкторской и научно-исследовательской работы. Можно очень четко описать задачу и данные, провести работу и не получить в итоге ничего, кроме знаний и экспертизы, - рассказывает Дмитрий Карагулян. - Сейчас есть проблема с тем, что монетизационная модель не просчитывается изначально». Цифровизироваться российской промышленности мешает, в числе прочего, тот факт, что существующий парк оборудования большей частью не поддерживает цифровизацию, считает Игорь Бевзюк: «Например, при изучении одного из кейсов российского агропромышленного комплекса оказалось, что только 20 процентов отечественной сельскохозяйственной техники поддерживает возможность получения автоматизированных заданий на внесение удобрений».
По словам Дениса Касимова, ключевой фактор для цифровизации - доступность данных: может отсутствовать система их передачи в онлайн-режиме, а в каких-то случаях не хватает самих датчиков. «Если, например, в электрическом двигателе снимается только два параметра, ток и напряжение, то уже сложно делать аналитику. Для нас это вызов - проводить качественный анализ, базируясь на имеющемся объеме данных. В России оснащенность датчиками пока ниже, чем на Западе». По мнению Алены Дробышевской, директора группы консультирования в области ИТ компании КПМГ в России и СНГ, западные страны во внедрении Big Data впереди, у них уже как минимум четыре года активно реализуются проекты цифровизации производства. Это связано с тем, что там промышленные предприятия раньше провели модернизацию. Второй фактор нашего отставания состоит в том, что работа с данными, Data Science, как профессиональная область в России только создается. Наконец, за рубежом предприятия просто-напросто дольше собирают данные, а для того, чтобы построить математическую модель, нужно аккумулировать информацию несколько месяцев или даже лет. Здесь стоит отметить, что в России есть интересные кейсы, когда предприятия много лет собирают данные. Например, один из производителей ферросплавов за семь лет собрал исторические данные более чем о двухстах тысячах плавок. В итоге был разработан программный продукт, который позволяет оптимально использовать дорогостоящие компоненты при выплавке. Это дает предприятию экономический эффект - ожидаемая годовая экономия составляет 275 млн рублей.
Разумеется, оборудование можно дооснастить датчиками, но это трудоемкий процесс, связанный с тем, что в какой-то момент необходимо остановить его работу; кроме того, с появлением новых датчиков оборудование снимается с гарантии. В железнодорожной отрасли, к примеру, для этого придется заново сертифицировать тип подвижного состава. А сертификация такого оборудования займет минимум полгода. «Но компании все равно идут на это, потому что иначе они просто технологически отстанут», - говорит Денис Касимов. Как поясняет Дмитрий Карагулян, для построения математической модели нужны качественные, не «пережатые», данные, а для этого в ряде случаев требуется менять настройки сбора данных или конфигурацию датчиков, а это критически важные параметры системы. Это и обусловливает сложность процесса съема информации.
Трудно говорить и о полной «импортонезависимости» российской отрасли Big Data, отмечает Игорь Бевзюк: в части компьютерной техники Россия в достаточно высокой степени зависит от импортного оборудования и ПО. «Общемировая практика показывает, что для работы с Big Data нужно общепромышленное высокопроизводительное оборудование, а отечественные микропроцессоры для обработки большого количества данных пока не подходят: они слишком дороги в пересчете на мощность, - говорит Игорь Бевзюк. - Сейчас в России инфраструктурное ПО оптимизируется под мировые стандарты оборудования. Но многие отечественные компании разрабатывают свои цифровые платформы».
Кроме того, по мнению аналитиков КПМГ, активный рост внедрения Big Data сдерживается тем, что российские компании реже, чем в Европе, Америке или странах Азии, используют облачные сервисы, руководствуясь соображениями безопасности данных, а в ряде случаев и требованиями законодательства. Облачная инфраструктура - это глобальный тренд, но Россия в этом смысле несколько отстает. Сейчас многие компании стоят перед выбором облака для хранения больших данных, отмечает Алексей Зенкевич из Honeywell. На первый взгляд частное корпоративное хранилище представляется более безопасным, поскольку данные остаются внутри компании. Однако такой подход требует значительных капитальных и эксплуатационных затрат: для компаний, использующих частное облако, аналитические сервисы обходятся дороже. К тому же в таком случае сложнее организовать обновление ПО и получать рекомендации внешних экспертов отрасли. А вот в отношении прикладных решений зависимость от импортного оборудования и ПО низкая, так как общеотраслевых универсальных решений пока нет: рынок только формируется и идет разработка продуктов, в том числе отечественных. «Например, то же решение Smart Maintenance, сегодня применяемое на локомотивах, завтра будет внедряться в энергетику и тяжелое машиностроение», - утверждает Игорь Бевзюк.
Все, что связано с цифровизацией, - это новые технологии, и здесь шансы российских разработчиков реализовать свои решения достаточно велики, считают участники формирующейся отрасли Big Data: с западными они примерно на одном уровне, а в чем-то и превосходят их.
«Передовиками» в использовании больших данных были разработчики поисковых систем, которые с помощью математического моделирования научились превращать поисковые запросы в реальные деньги. Возможно, теперь пришло время и промышленным предприятиям последовать их примеру. Тем более что в этой области у нас есть все шансы не отстать от западных стран.
В концепции «Индустрии 4.0» и в целом цифровизации производства именно Big Data становятся основой для принятия решений об изменениях процессов. Большими данными называют объемы информации, которые невозможно обработать традиционными способами, то есть с помощью обычного компьютера и в короткие сроки. Для работы с ними требуется специальное программное обеспечение и инфраструктура - центры обработки данных.
Впрочем, в России этот термин трактуется очень широко и, скорее, он похож на маркетинговый. Как отмечает Данила Целиканов, главный специалист по инновациям ПАО ММК, Big Data называют все, что связано с данными и математическими алгоритмами их обработки. В то время как классическое понимание термина предполагает наличие определенного объема информации - речь идет об огромных массивах данных, которых у большинства промышленных предприятий сегодня просто нет. «У нас нет больших данных в классическом понимании, - говорит Данила Целиканов. - Да, мы используем математические модели, строим их на неких массивах данных, накопившихся лет за десять. Но их нельзя назвать большими данными. Big Data у нас появятся, когда мы развернем проект в области интернета вещей, когда будут установлены тысячи полевых датчиков, с которых будут собираться терабайты информации».
По мнению Данилы Целиканова, оперировать большими данными могут ритейлеры с тысячами торговых точек и десятками тысяч наименований товара, сотовые операторы или энергетики с несколькими тысячами подстанций, с которых собирается цифровая информация. «Сейчас мы собираем данные, но, условно говоря, нам хватает сервера для их хранения и достаточно среды программирования R, чтобы их обработать, - говорит г-н Целиканов. - Это ничтожный объем по сравнению с цифровыми гигантами. Зато мы уже вовсю занимаемся матмоделированием и цифровыми двойниками».
Однако дело идет к тому, что к этому понятию - Big Data - металлурги вернутся буквально через три-пять лет, считает Данила Целиканов. Уже сейчас развиваются проекты в области интернета вещей, в этом году Магнитогорский металлургический комбинат, скорее всего, начнет тестировать сенсоры, которые будут размещаться на оборудовании. Если сейчас удается с помощью датчиков снимать информацию о полутора-двух процентах технологического процесса, говорит г-н Целиканов, то при развитии сенсоров и датчиков, возможностей использования локальных нейрочипов объем данных начнет быстро расти.
Если говорить о Big Data не в академически строгом понимании, то у российского бизнеса, как утверждает Дмитрий Карагулян, руководитель лаборатории по работе с большими данными (Big Data Lab) Фонда развития интернет-инициатив, в последние два года заметно растет интерес к сбору и анализу данных в «цифре». В течение первого года активно накапливалась экспертиза, а сегодня уже есть успешный опыт применения таких технологий, появилась возможность на основе работы с большими данными создавать продуктовые решения, применимые на производстве.
Как отмечают в 2050.Digital (разработчик решений для цифровизации), компании начинают понимать потенциальную ценность больших данных и рассматривать в том числе и «сырые» данные как полезный актив, даже если они не могут воспользоваться этой информацией прямо сейчас - построить предиктивные (предсказательные) модели или системы реагирования, работающие в режиме реального времени. Условия для работы с данными есть везде, где выстроен «нижний уровень» - система снятия параметров с оборудования и их регистрации. «На основании этих данных можно строить бесконечное количество моделей, но полезны будут только те, которые помогут решить конкретную проблему в бизнесе», - говорит Дмитрий Карагулян. Речь идет об аналитике, направленной либо на предиктивный анализ, либо на построение оптимальных бизнес-процессов.
Big Data существуют в тесной связке с интернетом вещей - вместе они позволяют производителям повысить связанность всех узлов производственной цепочки и бизнес-процессов в целом: например, научиться предсказывать необходимый состав сырья и колебания спроса и тут же перенастраивать производственные линии. Каким может быть эффект? Даже традиционный металлургический бизнес может изменить свое лицо: например, по-новому организовать сбыт и стать более ориентированным на розницу.
По мнению аналитиков аудиторско-консалтинговой компании КПМГ, сбором больших данных озаботились участники практически всех отраслей, хотя внедрение Big Data и происходит неравномерно. Если взять нефтяную отрасль, то здесь Big Data уже активно используются в геологоразведке и добыче, а вот переработка только начинает собирать данные.
По информации Алексея Зенкевича, руководителя подразделения «Промышленная автоматизация» компании Honeywell в России и странах Таможенного союза, одна из самых популярных областей применения больших данных в промышленности - мониторинг состояния оборудования. Анализируя информацию от датчиков, можно выявлять даже небольшие отклонения от нормального режима работы, быстро устранять причины снижения производительности и предотвращать вероятные поломки. С помощью предсказательной аналитики можно уйти от традиционной системы планово-предупредительных ремонтов, сокращать аварийные остановки и простои.
Дело в том, что с современных станков с числовым управлением можно «снять» большое количество данных, они снабжены десятками датчиков (реагирующих на температуру, вибрации, отслеживающих координаты деталей и т. д.). Как рассказывает Николай Петрухин, заместитель гендиректора ОАО «СТАН-сервис», современный комплекс датчиков в совокупности с системой обработки массивов информации позволяет отслеживать техническое состояние узлов и систем, заранее предупреждать пользователя об износах, необходимости проведения сервисных мероприятий. «Наибольший эффект от использования «умного» числового оборудования проявляется в случае объединения станочного парка участков, цехов, предприятий в единую сеть и их интеграции в глобальную ЕRP-систему предприятия. Объем анализируемых данных в этом случае возрастает в тысячи раз, и оптимизация работы оборудования, сокращение простоев, исключение брака позволяют кратно поднять производительность и уменьшить себестоимость продукции», - объясняет г-н Петрухин.
«Интерес к предиктивному анализу растет, - говорит Денис Касимов, гендиректор разработчика таких систем Clover Group (разработал систему «Умный локомотив» для группы компаний «Локотех»). - Но если говорить именно о тяжелой технике, то на рынке не много решений, готовых к внедрению».
Что касается оценок реального экономического эффекта от применения технологий мониторинга работоспособности оборудования, то, по словам Алексея Зенкевича, они помогают сократить на 10–15% время дорогостоящих простоев производства и снизить на пять процентов эксплуатационные затраты. Проекты, связанные с анализом данных об эффективности производственных процессов, окупаются за шесть-девять месяцев.
В этой области есть примеры. На Выксунском металлургическом заводе (входит в ОМК) автоматизировали планирование и управление ремонтными работами, чтобы сократить простои оборудования. В рамках проекта оборудование завода было снабжено NFC-метками на основе технологии идентификации путем беспроводной передачи данных. В компании говорят, что за первое полугодие работы системы они стали собирать почти в два с половиной раза больше данных о неисправностях оборудования, что позволило более адресно и своевременно проводить корректирующие мероприятия, чтобы не допускать внеплановых простоев. В то же время на 50% снизилось количество сообщений в системе о простоях оборудования и на 25% сократилась трудоемкость выполнения ремонтных работ.
Активно развивают проекты цифровизации Трансмашхолдинг и компания «Локотех», крупнейшая в России сервисная группа по обслуживанию и ремонту локомотивов. Программа цифровой трансформации включает в себя десятки различных инициатив, пилотные проекты уже запущены на Новочеркасском электровозостроительном заводе и в сервисном локомотивном депо (СЛД) Братское в Иркутской области.
«Цифровизация в депо Братское позволит нам правильно определить пути оптимизации технологических процессов и в целом повышения эффективности ремонтного производства посредством, например, изменения внутренних логистических потоков, расстановки персонала, уточнения последовательности выполнения ремонтных операций, оптимизации загрузки станков и оборудования, - рассказывает Игорь Бевзюк, гендиректор компании 2050.Digital, одного из участников проекта. - Сегодня внутри действующего депо отрабатывается порядка 200 цифровых решений, начиная с очков виртуальной реальности и заканчивая RFID-метками, которые используются во внутренней логистике и системах доступа». По словам Игоря Бевзюка, внедрение интеллектуальной системы «Цифровое депо» в СЛД Братское позволит повысить коэффициент технической готовности (КТГ) парка локомотивов на четыре процента, снизить операционные затраты на сервисное обслуживание на пять процентов, а неэксплуатируемый парк - на 25%.
Большие данные применяются и в целях прогнозирования спроса. Такую задачу ставит перед собой компания «Газпромнефть - смазочные материалы», которая в рамках внутреннего подразделения по machine learning (машинному обучению) разрабатывает систему анализа данных. Храниться и обрабатываться эти данные будут на платформе с открытым кодом доступа - open source, а значит, проблем не возникнет даже в случае санкционных ограничений. К разработкам впоследствии будут привлекать и крупных участников отрасли Big Data. Имея ассортимент продукции из 1500 позиций и 200 контрагентов в 76 странах, компания с помощью традиционных статистических инструментов не всегда могла четко прогнозировать спрос даже на месяц вперед. «В машинном обучении тоже заложен такой статистический механизм, но при этом система сама обучается каждый раз уточнять прогнозы и выявлять новые зависимости. В результате она может предугадывать то, что неподвластно жесткому алгоритму, который закладывается на базе формул по статистике», - объясняет Михаил Низкий, заместитель генерального директора по экономике и финансам компании «Газпромнефть - смазочные материалы». В этом году компания должна завершить сбор данных о продажах от контрагентов, аккумулировать их в большие данные, а в 2020 году планируется запустить проект по прогнозированию спроса.
Небольшая облачность
Но в целом цифровизация на производствах пока остается в зоне экспериментов. «Процентов на семьдесят технологии искусственного интеллекта состоят из опытно-конструкторской и научно-исследовательской работы. Можно очень четко описать задачу и данные, провести работу и не получить в итоге ничего, кроме знаний и экспертизы, - рассказывает Дмитрий Карагулян. - Сейчас есть проблема с тем, что монетизационная модель не просчитывается изначально». Цифровизироваться российской промышленности мешает, в числе прочего, тот факт, что существующий парк оборудования большей частью не поддерживает цифровизацию, считает Игорь Бевзюк: «Например, при изучении одного из кейсов российского агропромышленного комплекса оказалось, что только 20 процентов отечественной сельскохозяйственной техники поддерживает возможность получения автоматизированных заданий на внесение удобрений».
По словам Дениса Касимова, ключевой фактор для цифровизации - доступность данных: может отсутствовать система их передачи в онлайн-режиме, а в каких-то случаях не хватает самих датчиков. «Если, например, в электрическом двигателе снимается только два параметра, ток и напряжение, то уже сложно делать аналитику. Для нас это вызов - проводить качественный анализ, базируясь на имеющемся объеме данных. В России оснащенность датчиками пока ниже, чем на Западе». По мнению Алены Дробышевской, директора группы консультирования в области ИТ компании КПМГ в России и СНГ, западные страны во внедрении Big Data впереди, у них уже как минимум четыре года активно реализуются проекты цифровизации производства. Это связано с тем, что там промышленные предприятия раньше провели модернизацию. Второй фактор нашего отставания состоит в том, что работа с данными, Data Science, как профессиональная область в России только создается. Наконец, за рубежом предприятия просто-напросто дольше собирают данные, а для того, чтобы построить математическую модель, нужно аккумулировать информацию несколько месяцев или даже лет. Здесь стоит отметить, что в России есть интересные кейсы, когда предприятия много лет собирают данные. Например, один из производителей ферросплавов за семь лет собрал исторические данные более чем о двухстах тысячах плавок. В итоге был разработан программный продукт, который позволяет оптимально использовать дорогостоящие компоненты при выплавке. Это дает предприятию экономический эффект - ожидаемая годовая экономия составляет 275 млн рублей.
Разумеется, оборудование можно дооснастить датчиками, но это трудоемкий процесс, связанный с тем, что в какой-то момент необходимо остановить его работу; кроме того, с появлением новых датчиков оборудование снимается с гарантии. В железнодорожной отрасли, к примеру, для этого придется заново сертифицировать тип подвижного состава. А сертификация такого оборудования займет минимум полгода. «Но компании все равно идут на это, потому что иначе они просто технологически отстанут», - говорит Денис Касимов. Как поясняет Дмитрий Карагулян, для построения математической модели нужны качественные, не «пережатые», данные, а для этого в ряде случаев требуется менять настройки сбора данных или конфигурацию датчиков, а это критически важные параметры системы. Это и обусловливает сложность процесса съема информации.
Трудно говорить и о полной «импортонезависимости» российской отрасли Big Data, отмечает Игорь Бевзюк: в части компьютерной техники Россия в достаточно высокой степени зависит от импортного оборудования и ПО. «Общемировая практика показывает, что для работы с Big Data нужно общепромышленное высокопроизводительное оборудование, а отечественные микропроцессоры для обработки большого количества данных пока не подходят: они слишком дороги в пересчете на мощность, - говорит Игорь Бевзюк. - Сейчас в России инфраструктурное ПО оптимизируется под мировые стандарты оборудования. Но многие отечественные компании разрабатывают свои цифровые платформы».
Кроме того, по мнению аналитиков КПМГ, активный рост внедрения Big Data сдерживается тем, что российские компании реже, чем в Европе, Америке или странах Азии, используют облачные сервисы, руководствуясь соображениями безопасности данных, а в ряде случаев и требованиями законодательства. Облачная инфраструктура - это глобальный тренд, но Россия в этом смысле несколько отстает. Сейчас многие компании стоят перед выбором облака для хранения больших данных, отмечает Алексей Зенкевич из Honeywell. На первый взгляд частное корпоративное хранилище представляется более безопасным, поскольку данные остаются внутри компании. Однако такой подход требует значительных капитальных и эксплуатационных затрат: для компаний, использующих частное облако, аналитические сервисы обходятся дороже. К тому же в таком случае сложнее организовать обновление ПО и получать рекомендации внешних экспертов отрасли. А вот в отношении прикладных решений зависимость от импортного оборудования и ПО низкая, так как общеотраслевых универсальных решений пока нет: рынок только формируется и идет разработка продуктов, в том числе отечественных. «Например, то же решение Smart Maintenance, сегодня применяемое на локомотивах, завтра будет внедряться в энергетику и тяжелое машиностроение», - утверждает Игорь Бевзюк.
Все, что связано с цифровизацией, - это новые технологии, и здесь шансы российских разработчиков реализовать свои решения достаточно велики, считают участники формирующейся отрасли Big Data: с западными они примерно на одном уровне, а в чем-то и превосходят их.
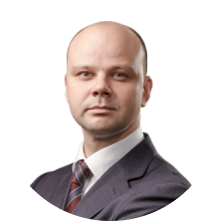
Читайте еще