Конец мартеновской эпохи
26.03.2018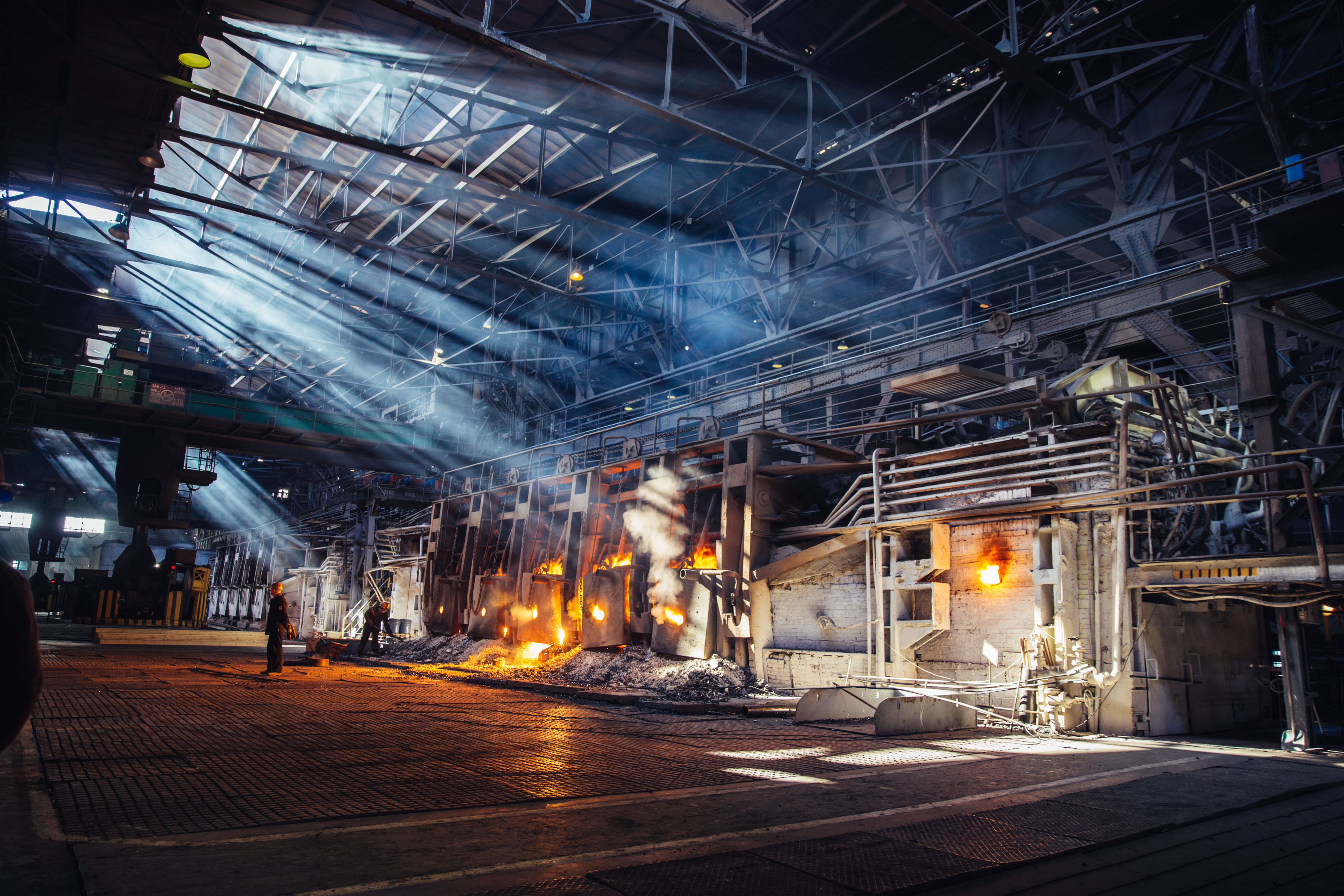
Прекратила работу последняя крупная мартеновская печь в России
На Выксунском металлургическом заводе (ВМЗ) в Нижегородской области, входящем в состав Объединенной металлургической компании, (ОМК), закрывается мартеновская печь. Последняя плавка проведена 23 марта. Завершилась почти полуторавековая эпоха в истории отечественной металлургии.
Сталеплавильный цех ВМЗ общей мощностью около 500 тыс. тонн стали в год состоял из двух мартеновских печей, по 250 тыс. тонн на каждую. Производимая сталь использовалась для выпуска железнодорожных колес. Фактически в 2016 году, по данным компании, цех произвел 200 тыс. тонн мартеновской стали. Одна из печей была поставлена на горячую консервацию еще в 2014 году, когда в России снизилось потребление колесной продукции.
В современном виде цех существовал с 1974 года, когда в ходе коренной реконструкции ВМЗ он и был переориентирован на обеспечение потребностей колесопрокатного комплекса. Хотя раньше мартеновских печей здесь было три — третью демонтировали в ходе модернизации цеха еще в 2004–2005 годах. На ее месте создан полностью автоматизированный участок внепечной обработки стали в составе установки «печь–ковш» и вакууматора камерного типа, что позволило повысить производительность и качество продукции. Использование кислорода дало возможность снизить продолжительность плавок и увеличить период между ремонтами печей.
Всего к марту этого года в цехе было проведено более 107 тыс. плавок, получено почти 25 млн тонн мартеновской стали. А теперь этому пришел конец.
«В основе этого решения — новые возможности для устойчивого развития компании, — говорит руководитель департамента по развитию активов и инвестициям ОМК Дмитрий Чернышев. — Это возможность закрыть старое производство и улучшить экологию в городе Выксе. Выксунский металлургический завод — градообразующее предприятие. Компания выступает системным партнером моногорода, вкладывая средства в улучшение городской среды. С остановкой мартеновской печи практически полностью прекратятся выбросы предприятия в атмосферу Выксы».
Кроме того, уверяет Дмитрий Чернышев, это возможность улучшить условия труда сотрудников сталеплавильного цеха ВМЗ: «Работа в мартеновском цехе — тяжелая, порой даже опасная. Теперь практически все триста сотрудников мартеновского цеха переходят на современные рабочие места на заводе, в том числе в совершенно новый трубный цех, который сейчас строится в Выксе, а также на современный литейно-прокатный комплекс».
Колесопрокатный комплекс при этом продолжит работать — на покупной стали. В ОМК утверждают, что с переходом колесопрокатного комплекса ВМЗ на сталь, выпущенную в электропечах, компания даже получила технологическую возможность расширить сортамент и области применения железнодорожных колес.
Схема мартеновской печи
После штукофена
Человечество производит изделия из железа уже примерно три тысячи лет, историки даже выделили в мировой истории особую эпоху — железный век. Большую часть этого времени технологии использовались довольно примитивные — одноразовая сыродутная печи и последующая ковка заготовки.
В XIII веке в Германии получили распространение постоянные металлургические печи — штукофены. Они имели сравнительно небольшие размеры (от трех до пяти метров в высоту, чуть больше метра в диаметре), но обладали неплохой для доиндустриальной эпохи производительностью — до 250 килограммов железа в день. Правда, недостатком этой технологии была довольно высокая (до 10%) доля отходов — штукофен по своему устройству был схож с доменной печью в миниатюре и выдавал в том числе чугун, а вот его кузнецы обрабатывать не умели.
Нечто похожее на индустриальное производство в черной металлургии началось с появлением доменных печей. Первые такие печи появились во второй половине XV века в Вестфалии, на западе Германии. В России первая доменная печь была устроена в Туле в 1632 году усилиями заводчика Андрея Виниуса.
С распространением доменного производства получил развитие и передельный процесс — переработка чугуна в сталь. До XVIII века доминирующей технологией был обжиг в горнах с использованием древесного угля. Технологии развивались — например, расход энергии на изготовление тонны стали в горне с середины XVI до середины XVIII века сократился в четыре раза. В 1718 году в Великобритании впервые был применен кокс.
С конца XVIII века получает распространение технология пудлингования — расплавление чугуна в специальной печи без контакта с топливом и перемешивание расплавленного металла специальными штангами, на которых налипают частички расплавленного железа, постепенно формируя тестоподобную крицу массой до 60 килограммов.
В 1855 году английский инженер Генри Бессемер получил патент на еще более совершенный метод получения стали — путем продувки чугуна в конвертере. Технология стала известна как бессемеровский процесс. В 1860 году был построен первый бессемеровский конвертер, после чего технология начала свое победное шествие по всему миру.
Бессемеровский процесс позволял получать сталь быстро (примерно за 15 минут) и сравнительно дешево. Но поскольку чугун продувался обычным атмосферным воздухом, который большей частью состоит из азота, полученная сталь отличалась повышенным содержанием азота, а потому и повышенной хрупкостью.
В 1878 году английский инженер Сидни Томас предложил еще одну разновидность конвертера, позволявшую перерабатывать чугун с высоким содержанием фосфора. Эта технология тоже получила широкое распространение, успешно конкурировала с бессемеровским процессом и в конце XIX века уступала по объемам производства только ему. Но томасовская сталь имела те же недостатки, что и бессемеровская: сравнительно высокую хрупкость.
Явление мартена
Проблема контроля качества получаемой стали была решена в мартеновских печах.
Впервые эта технология была предложена немецким инженером Карлом Сименсом в 1864 году. В 1865-м французский инженер Пьер-Эмиль Мартен приобрел у Сименса лицензию на его изобретение и впервые на практике использовал ее для выплавки стали. По сравнению со своими «потомками» из XX века первая печь Мартена была совсем небольшой, всего на полторы тонны металла. Сталь, полученная в этой печи, отличалась хорошим качеством и была удостоена премии Всемирной парижской выставки 1867 года.
В отличие от конвертеров в мартеновской печи можно использовать в качестве сырья (шихты) как чугун любого состава, так и стальной лом, причем в любой пропорции. В позднем Советском Союзе, например, на одну тонну мартеновской стали использовали в среднем 580–590 килограммов чугуна и 480–490 килограммов лома.
По сравнению с продувкой чугуна в конвертере мартеновский процесс занимает весьма продолжительное время — до восьми часов на одну плавку. Зато появляется возможность существенно расширить сырьевую базу (например, за счет массовой переплавки лома) и контролировать ход процесса, получить сталь с заданными свойствами. Это и стало причиной его широкого распространения.
Заведующий лабораторией электроплавки института металлургии и машиностроения Государственного научного центра НПО «ЦНИИТмаш» Анатолий Куликов рассказывает: «В отличие от конвертерных способов получения стали мартеновский процесс был не слишком требователен к химическому составу исходного материала, позволял переплавлять большое количество стального лома, а качество мартеновской стали было выше. Однако плавка в мартеновской печи занимает гораздо больше времени, чем в конвертере. Мартеновская печь требует внешнего обогрева в течение всей плавки, в то время как конвертер разогревается сам. Достоинством стали, выплавленной в мартеновской печи в девятнадцатом и в начале двадцатого века, по сравнению с конвертерной, был ее большой ассортимент, в то время как для увеличения количества марок стали конвертерной используют установку доводки стали. К середине двадцатого века мартеновским способом изготовлялось около 80 процентов стали, производимой в мире».
Мартеновская печь представляет собой сооружение из огнеупорного кирпича, усиленное рядом металлических балок, которые образуют внешний каркас. Рабочее пространство печи ограничено сверху сводом, снизу — подом, спереди и сзади — стенками, по бокам — головками. Головки служат для подачи топлива и воздуха в рабочее пространство печи, а также для отвода из нее продуктов сгорания. Печь имеет вид овальной чаши, в ней происходит процесс плавки. Передняя стенка имеет ряд окон для загрузки шихтовых материалов, а задняя — клетку для выпуска металла.
В основе процесса мартеновской плавки лежат окислительные процессы, в результате которых из шихты получают жидкую сталь заданного состава. В мартеновских печах плавка идет за счет тепла пламени, образующегося при горении в рабочем пространстве печи смеси доменного и коксового газов.
При попадании в рабочее пространство печи газ соприкасается с воздухом и воспламеняется. Под действием этого тепла шихта нагревается и плавится. Одновременно с расплавлением металла происходит окисление его основных компонентов. Основной окислитель — кислород, который засасывается в рабочее пространство печи из атмосферы. Железо шихты при окислении переходит в закись железа, а примеси — в соответствующие оксиды: кремнезем, закись марганца, окись углерода и т. п. Окись углерода удаляется из печи с дымовыми газами, остальные примеси переходят в шлак. Перемешивание металла при выделении пузырьков окиси углерода способствует окислению примесей. Когда металл покрывается слоем шлака, непосредственное окисление примесей кислородом воздуха становится невозможным, и дальнейшее окисление протекает за счет закиси железа.
Добавление в шихту флюсов (извести или известняка) способствует удалению из металла серы и фосфора. Затем шлак, образовавшийся при плавке, сливают. Во время плавки берутся пробы металла для определения его химического состава и, при необходимости, доведения этого состава до требуемого. Когда металл доведен до нужного состава, в него вводят раскислители (обычно ферросплавы), чтобы отобрать кислород у закиси железа. Если нужно, после раскисления вводят легирующие элементы: ферротитан, феррохром, высококремнистый ферросилиций, чистый никель и другие. После чего сталь выпускают из печи в ковш.
Россия не оставалась в стороне от прогресса. Первая мартеновская печь в нашей стране была запущена уже 16 марта 1870 года на Сормовском заводе в Нижегородской губернии. Причем печь была построена силами русских специалистов во главе с инженером Александром Износковым. Мартеновские печи на Сормовском заводе проработали до 1998 года.
А после Сормова новые мартеновские печи стали расти и в других точках нашей страны.
Самая первая мартеновская печь в Выксе была построена в 1892 году в пудлинговом цехе Нижне-Выксунского завода (на тот момент он был частью «Общества выксунских горных заводов»). С 1904 года мартеновский способ производства стал в Выксе единственным (хотя на отдельных предприятиях СССР пудлингование применялось до 1930-х), при этом заводы стали называться металлургическими.
С 1920 года выксунские заводы вошли в Приокский горный округ. После окончания Гражданской войны в 1921 году заводы округа давали 7,2% чугуна, 10,9% стали и проката, производимых в РСФСР. Тогда же перед заводами округа была поставлена задача участвовать в восстановлении разрушенной транспортной системы страны: требовалось производить рельсы, сортовой прокат, лист, бандажи и трубы для производства вагонов и паровозов, строительства путей и мостов.
В 1933 году в Выксе была произведена первая плавка в новом мартеновском (ныне — сталеплавильном) цехе № 2, так что осенью этого года цех отметил бы 85 лет. Но уже не отметит. Теперь мартеновские печи останутся только в знаменитой песне.
Последний день работы мартеновского цеха Выксунского металлургического завода
Смена уклада
Ударом по мартену стало развитие новых технологий получения стали во второй половине XX века.
Во-первых, технический прогресс позволил получать в промышленных масштабах чистый кислород, что сразу перевернуло соотношение сил между мартеном и конвертерами. Первые эксперименты с применением чистого кислорода для плавки были проведены еще в 1933–1936 годах в Киеве под руководством инженера Николая Мозгового. А с 1952 года технология стала использоваться в массовом промышленном производстве на заводах австрийской металлургической компании VOEST. Собственно, технология использования кислородных конвертеров известна также под альтернативным именем «процесс Линц—Донавитц», в честь двух австрийских городов, где впервые были построены промышленные кислородные конвертеры.
Кислородный конвертер позволял получать сталь в десять раз быстрее мартена, он отличается гораздо более высокой энергоэффективностью (мартеновская печь требует внешнего обогрева в течение всей плавки, конвертер разогревается сам). А использование чистого кислорода позволило избавиться от давней «болезни» бессемеровского и томасовского процессов — дополнительных примесей в стали и возможности плавить только чугун (кислородному конвертеру за счет более высокой окислительной способности чистого кислорода по зубам и смесь чугуна с ломом).
Вторым фактором против мартена стало развитие электрометаллургии. Первые экспериментальные электродуговые печи были построены еще в 1870-х годах. По иронии судьбы патент на электродуговую печь получил все тот же Карл Сименс — фактический изобретатель мартеновской печи. В 1907 году под руководством французского инженера Поля Эру был построен первый электрометаллургический завод в США. Если конвертер требует преимущественно чугуна, то электродуговая печь может взять на себя переплавку «излишков» лома. Долгое время распространение технологии упиралось в ограничение мощностей электрогенерации. Но во второй половине XX века мир увидел как взрывной рост электроэнергетики, так и совершенствование самой технологии электрометаллургии. Если в 1965 году электродуговая печь на тонну стали требовала 630 киловатт электроэнергии и 6,5 килограмма электродов, то к 1990-м этот показатель опустился до 350 киловатт и 2,2 килограмма.
Наконец, третьим технологическим аргументом против мартена стало распространение во второй половине XX века машин непрерывного литья заготовки (МНЛЗ). В 1952 году был выдан первый патент на машину подобного типа, к 1970-м МНЛЗ получили широчайшее распространение в металлургии развитых стран, а затем стали непременным атрибутом мировой металлургии вообще. И с мартеном, из-за специфики его плавки, МНЛЗ оказалась довольно плохо совместима.
И с 1970-х строить новые мартеновские печи в мире прекратили.
«Во второй половине XX века, с появлением мощных электродуговых печей и установок внепечной обработки стали с электроподогревом жидкой стали с последующим вакуумированием или продувкой инертными газами, а также с появлением широкой возможности автоматизации электропечей и установок внепечной металлургии, производство сталей получает новый виток и выходит на более качественный уровень по содержанию вредных примесей и газов. Таким образом, общая совокупность развития конвертерной и электростали, а также быстрота получения больших объемов жидкой стали и автоматизации процессов производства вытеснила мартеновское производство в большинстве стран мира», — говорит Анатолий Куликов.
Действительно, по данным Мировой ассоциации производителей стали (WSA), объем производства мартеновской стали в мире сократился с 195,4 млн тонн в 1974 году до 6,8 млн тонн в 2016-м. Доля мартеновского производства в общем объеме мировой выплавки стали за тот же временной период сократилась с 30% менее чем до 0,5%.
Ранее столь же обвальное падение наблюдалось при уходе мировой металлургии от бессемеровского процесса.
Снижение роли мартеновского производства наблюдалось и в нашей стране. Если в 1974 году на мартены пришлось 67% всей советской стали, то в 1990-м — чуть более 51%.
В Советском Союзе поднимался вопрос о возможности физического прекращения мартеновского производства. Но, как следует из выкладок советских экономистов, перепрофилирование средних размеров металлургического предприятия с мартенов на конвертеры стоило бы порядка 100–110 млн рублей в ценах конца 1970-х годов. И в условиях довольно наплевательского отношения к окружающей среде и планово дешевых энергоносителей это сочли нецелесообразным.
Загрузка металлургических мощностей в мире
Рынок решил
Ситуация принципиально изменилась с переходом экономики России на рыночные рельсы и повышением внимания к экологии. Часть печей была остановлена из экономических соображений. В ряде случаев за невидимой рукой рынка явно маячила тень правительства. Так, в 2013 году Минпромторг стал настаивать на выводе из эксплуатации всех мартеновских печей еще до конца 2015 года. «На мартеновское производство в 2013 году в России приходилось 28 процентов промышленных выбросов в атмосферу и свыше шести процентов сброса сточных вод», — говорил замминистра Глеб Никитин. В качестве альтернативы министерство предлагало строить электропечи.
Например, «Северсталь» полностью отказалась от мартеновских печей (а их в Череповце было 12!) в 2011 году, ММК — в 2003 году, «Евраз» - в 2006-м.
«Если сравнивать затраты на производство стали в мартене или, скажем, в дуговой печи, то при прочих равных затраты будут одного порядка, — говорит Дмитрий Чернышев. — Но за счет большего числа переделов и несовершенного способа разливки мартеновский способ по эффективности уступает электросталеплавильному. Это “отступление” мы наблюдали последние годы в мировой металлургии. Мы также понимали, что мартеновский способ морально устарел, что он вреден для экологии, поэтому давно ждали возможности уйти от его использования».
Как отмечают в компании, инвестиции в строительство собственных дополнительных сталеплавильных мощностей в Выксе для производства колес экономически неоправданны (у ВМЗ есть литейно-прокатный комплекс по выпуску горячекатаного проката мощностью 1,2 млн тонн, вся продукция которого перерабатывается в трубы среднего и малого диаметра).
«В течение нескольких лет мы искали внешнего поставщика стали. И как только был найден надежный партнер, мы приняли долгожданное решение об остановке мартена, — рассказывает Дмитрий Чернышев. — Таким образом, двигаясь в русле курса России на ужесточение природоохранных требований, мы решили наболевший экологический вопрос в Выксе, а параллельно и проблему использования устаревших технологий разливки в изложницы: необходимость соответствовать определенным требованиям накладывала непреодолимые ограничения на применение мартеновской стали для выпуска некоторой колесной продукции».
Отметим, что в общей сложности в России объем производства мартеновской стали упал с 33,5 млн тонн в 1992 году до 1,6 млн тонн в 2016-м. Доля мартена в общенациональной выплавке стали за тот же период сократилась с 50 до 2,4%. То есть все самое главное уже произошло — закрытие выксунского мартена лишь ставит точку в уже свершившемся переходе.
Теперь практически все мировое мартеновское производство оказывается сосредоточено на Украине, которая все больше превращается в заповедник архаичных технологий.
После мартена
Колесопрокатное производство ВМЗ после закрытия мартена перейдет на сталь сторонних поставщиков. В начале 2017 года ОМК уже заключила долгосрочный (на десять лет) контракт с «Уральской сталью».
«В партнеры по обеспечению колесного производства сталью был выбран завод “Уральская сталь” из города Новотроицка Оренбургской области, — рассказывает руководитель коммерческого департамента ОМК Эдуард Степанцов. — Потребность в сырье колесопрокатного производства ВМЗ при полной загрузке составляет около 400 тысяч тонн стали в год».
Эдуард Степанцов уверяет, что закрытие мартена в Выксе не приведет к перебоям в поставках железнодорожных колес. Общие производственные мощности производителей в Евразийском экономическом союзе на 2018 год составляют порядка 1,5 млн штук в год, в том числе 850 тыс. — у ВМЗ. По оценке ОМК, основанной на производстве вагонов в 2017 году, заявлениях вагоностроителей и статистике потребления, максимальная потребность в колесах на рынке Союза в 2018-2019 годах может составить не более 1,47 млн штук в год. Поэтому существующие внутренние мощности способны полностью удовлетворить потребности в колесах. Не пострадает и качество продукции.
«Сегодня иная ситуация. Независимо от того, каким способом идет производство стали, ее качество, если говорить упрощенно, достигается исходным сырьем и путем так называемого доведения по химическому составу — ее дополнительной обработкой вне печи, — рассказывает Дмитрий Чернышев. — Сталеплавильный цех ВМЗ в составе мартеновской печи и современного комплекса внепечной обработки стали — печи–ковша и вакууматора, введенных в строй в 2005 году, был способен производить сталь в полном соответствии с требованиями по качеству. Но лучшая альтернатива мартену, вне сомнения, современное электросталеплавильное производство».
Перед мировой металлургической отраслью сохраняется проблема неполной загрузки мощностей (см. график 4). Более того, конкуренция производителей может обостряться за счет того, что с распространением альтернативных конструкционных материалов сжимается потенциальный рынок для стали. Например, содержание стали в автомобиле сократилось с 86% по массе в 1980-х до 66% в 2000-х и продолжает снижаться. Даже рост мировой экономики все слабее коррелирует с динамикой стального рынка (см. график 5).
Ответом на эти вызовы может быть все возрастающее внимание к технологичности производства. В частности, Анатолий Куликов полагает, что в перспективе можно ожидать еще одного технологического перехода в отрасли: «Открытие мини-заводов на основе высокопроизводительных электропечей представляет более широкие возможности, чем конвертерное производство. Уже сейчас время расплавления и массы плавок конвертеров и электропечей сопоставимы. Производство электростали с использованием технологий вторичной металлургии более мобильно и экологично по сравнению с конвертерным производством, а уровень автоматизации получения электростали находится на высоком уровне».
На Выксунском металлургическом заводе (ВМЗ) в Нижегородской области, входящем в состав Объединенной металлургической компании, (ОМК), закрывается мартеновская печь. Последняя плавка проведена 23 марта. Завершилась почти полуторавековая эпоха в истории отечественной металлургии.
Сталеплавильный цех ВМЗ общей мощностью около 500 тыс. тонн стали в год состоял из двух мартеновских печей, по 250 тыс. тонн на каждую. Производимая сталь использовалась для выпуска железнодорожных колес. Фактически в 2016 году, по данным компании, цех произвел 200 тыс. тонн мартеновской стали. Одна из печей была поставлена на горячую консервацию еще в 2014 году, когда в России снизилось потребление колесной продукции.
В современном виде цех существовал с 1974 года, когда в ходе коренной реконструкции ВМЗ он и был переориентирован на обеспечение потребностей колесопрокатного комплекса. Хотя раньше мартеновских печей здесь было три — третью демонтировали в ходе модернизации цеха еще в 2004–2005 годах. На ее месте создан полностью автоматизированный участок внепечной обработки стали в составе установки «печь–ковш» и вакууматора камерного типа, что позволило повысить производительность и качество продукции. Использование кислорода дало возможность снизить продолжительность плавок и увеличить период между ремонтами печей.
Всего к марту этого года в цехе было проведено более 107 тыс. плавок, получено почти 25 млн тонн мартеновской стали. А теперь этому пришел конец.
«В основе этого решения — новые возможности для устойчивого развития компании, — говорит руководитель департамента по развитию активов и инвестициям ОМК Дмитрий Чернышев. — Это возможность закрыть старое производство и улучшить экологию в городе Выксе. Выксунский металлургический завод — градообразующее предприятие. Компания выступает системным партнером моногорода, вкладывая средства в улучшение городской среды. С остановкой мартеновской печи практически полностью прекратятся выбросы предприятия в атмосферу Выксы».
Кроме того, уверяет Дмитрий Чернышев, это возможность улучшить условия труда сотрудников сталеплавильного цеха ВМЗ: «Работа в мартеновском цехе — тяжелая, порой даже опасная. Теперь практически все триста сотрудников мартеновского цеха переходят на современные рабочие места на заводе, в том числе в совершенно новый трубный цех, который сейчас строится в Выксе, а также на современный литейно-прокатный комплекс».
Колесопрокатный комплекс при этом продолжит работать — на покупной стали. В ОМК утверждают, что с переходом колесопрокатного комплекса ВМЗ на сталь, выпущенную в электропечах, компания даже получила технологическую возможность расширить сортамент и области применения железнодорожных колес.
Схема мартеновской печи
После штукофена
Человечество производит изделия из железа уже примерно три тысячи лет, историки даже выделили в мировой истории особую эпоху — железный век. Большую часть этого времени технологии использовались довольно примитивные — одноразовая сыродутная печи и последующая ковка заготовки.
В XIII веке в Германии получили распространение постоянные металлургические печи — штукофены. Они имели сравнительно небольшие размеры (от трех до пяти метров в высоту, чуть больше метра в диаметре), но обладали неплохой для доиндустриальной эпохи производительностью — до 250 килограммов железа в день. Правда, недостатком этой технологии была довольно высокая (до 10%) доля отходов — штукофен по своему устройству был схож с доменной печью в миниатюре и выдавал в том числе чугун, а вот его кузнецы обрабатывать не умели.
Нечто похожее на индустриальное производство в черной металлургии началось с появлением доменных печей. Первые такие печи появились во второй половине XV века в Вестфалии, на западе Германии. В России первая доменная печь была устроена в Туле в 1632 году усилиями заводчика Андрея Виниуса.
С распространением доменного производства получил развитие и передельный процесс — переработка чугуна в сталь. До XVIII века доминирующей технологией был обжиг в горнах с использованием древесного угля. Технологии развивались — например, расход энергии на изготовление тонны стали в горне с середины XVI до середины XVIII века сократился в четыре раза. В 1718 году в Великобритании впервые был применен кокс.
С конца XVIII века получает распространение технология пудлингования — расплавление чугуна в специальной печи без контакта с топливом и перемешивание расплавленного металла специальными штангами, на которых налипают частички расплавленного железа, постепенно формируя тестоподобную крицу массой до 60 килограммов.
В 1855 году английский инженер Генри Бессемер получил патент на еще более совершенный метод получения стали — путем продувки чугуна в конвертере. Технология стала известна как бессемеровский процесс. В 1860 году был построен первый бессемеровский конвертер, после чего технология начала свое победное шествие по всему миру.
Бессемеровский процесс позволял получать сталь быстро (примерно за 15 минут) и сравнительно дешево. Но поскольку чугун продувался обычным атмосферным воздухом, который большей частью состоит из азота, полученная сталь отличалась повышенным содержанием азота, а потому и повышенной хрупкостью.
В 1878 году английский инженер Сидни Томас предложил еще одну разновидность конвертера, позволявшую перерабатывать чугун с высоким содержанием фосфора. Эта технология тоже получила широкое распространение, успешно конкурировала с бессемеровским процессом и в конце XIX века уступала по объемам производства только ему. Но томасовская сталь имела те же недостатки, что и бессемеровская: сравнительно высокую хрупкость.
Явление мартена
Проблема контроля качества получаемой стали была решена в мартеновских печах.
Впервые эта технология была предложена немецким инженером Карлом Сименсом в 1864 году. В 1865-м французский инженер Пьер-Эмиль Мартен приобрел у Сименса лицензию на его изобретение и впервые на практике использовал ее для выплавки стали. По сравнению со своими «потомками» из XX века первая печь Мартена была совсем небольшой, всего на полторы тонны металла. Сталь, полученная в этой печи, отличалась хорошим качеством и была удостоена премии Всемирной парижской выставки 1867 года.
В отличие от конвертеров в мартеновской печи можно использовать в качестве сырья (шихты) как чугун любого состава, так и стальной лом, причем в любой пропорции. В позднем Советском Союзе, например, на одну тонну мартеновской стали использовали в среднем 580–590 килограммов чугуна и 480–490 килограммов лома.
По сравнению с продувкой чугуна в конвертере мартеновский процесс занимает весьма продолжительное время — до восьми часов на одну плавку. Зато появляется возможность существенно расширить сырьевую базу (например, за счет массовой переплавки лома) и контролировать ход процесса, получить сталь с заданными свойствами. Это и стало причиной его широкого распространения.
Заведующий лабораторией электроплавки института металлургии и машиностроения Государственного научного центра НПО «ЦНИИТмаш» Анатолий Куликов рассказывает: «В отличие от конвертерных способов получения стали мартеновский процесс был не слишком требователен к химическому составу исходного материала, позволял переплавлять большое количество стального лома, а качество мартеновской стали было выше. Однако плавка в мартеновской печи занимает гораздо больше времени, чем в конвертере. Мартеновская печь требует внешнего обогрева в течение всей плавки, в то время как конвертер разогревается сам. Достоинством стали, выплавленной в мартеновской печи в девятнадцатом и в начале двадцатого века, по сравнению с конвертерной, был ее большой ассортимент, в то время как для увеличения количества марок стали конвертерной используют установку доводки стали. К середине двадцатого века мартеновским способом изготовлялось около 80 процентов стали, производимой в мире».
Мартеновская печь представляет собой сооружение из огнеупорного кирпича, усиленное рядом металлических балок, которые образуют внешний каркас. Рабочее пространство печи ограничено сверху сводом, снизу — подом, спереди и сзади — стенками, по бокам — головками. Головки служат для подачи топлива и воздуха в рабочее пространство печи, а также для отвода из нее продуктов сгорания. Печь имеет вид овальной чаши, в ней происходит процесс плавки. Передняя стенка имеет ряд окон для загрузки шихтовых материалов, а задняя — клетку для выпуска металла.
В основе процесса мартеновской плавки лежат окислительные процессы, в результате которых из шихты получают жидкую сталь заданного состава. В мартеновских печах плавка идет за счет тепла пламени, образующегося при горении в рабочем пространстве печи смеси доменного и коксового газов.
При попадании в рабочее пространство печи газ соприкасается с воздухом и воспламеняется. Под действием этого тепла шихта нагревается и плавится. Одновременно с расплавлением металла происходит окисление его основных компонентов. Основной окислитель — кислород, который засасывается в рабочее пространство печи из атмосферы. Железо шихты при окислении переходит в закись железа, а примеси — в соответствующие оксиды: кремнезем, закись марганца, окись углерода и т. п. Окись углерода удаляется из печи с дымовыми газами, остальные примеси переходят в шлак. Перемешивание металла при выделении пузырьков окиси углерода способствует окислению примесей. Когда металл покрывается слоем шлака, непосредственное окисление примесей кислородом воздуха становится невозможным, и дальнейшее окисление протекает за счет закиси железа.
Добавление в шихту флюсов (извести или известняка) способствует удалению из металла серы и фосфора. Затем шлак, образовавшийся при плавке, сливают. Во время плавки берутся пробы металла для определения его химического состава и, при необходимости, доведения этого состава до требуемого. Когда металл доведен до нужного состава, в него вводят раскислители (обычно ферросплавы), чтобы отобрать кислород у закиси железа. Если нужно, после раскисления вводят легирующие элементы: ферротитан, феррохром, высококремнистый ферросилиций, чистый никель и другие. После чего сталь выпускают из печи в ковш.
Россия не оставалась в стороне от прогресса. Первая мартеновская печь в нашей стране была запущена уже 16 марта 1870 года на Сормовском заводе в Нижегородской губернии. Причем печь была построена силами русских специалистов во главе с инженером Александром Износковым. Мартеновские печи на Сормовском заводе проработали до 1998 года.
А после Сормова новые мартеновские печи стали расти и в других точках нашей страны.
Самая первая мартеновская печь в Выксе была построена в 1892 году в пудлинговом цехе Нижне-Выксунского завода (на тот момент он был частью «Общества выксунских горных заводов»). С 1904 года мартеновский способ производства стал в Выксе единственным (хотя на отдельных предприятиях СССР пудлингование применялось до 1930-х), при этом заводы стали называться металлургическими.
С 1920 года выксунские заводы вошли в Приокский горный округ. После окончания Гражданской войны в 1921 году заводы округа давали 7,2% чугуна, 10,9% стали и проката, производимых в РСФСР. Тогда же перед заводами округа была поставлена задача участвовать в восстановлении разрушенной транспортной системы страны: требовалось производить рельсы, сортовой прокат, лист, бандажи и трубы для производства вагонов и паровозов, строительства путей и мостов.
В 1933 году в Выксе была произведена первая плавка в новом мартеновском (ныне — сталеплавильном) цехе № 2, так что осенью этого года цех отметил бы 85 лет. Но уже не отметит. Теперь мартеновские печи останутся только в знаменитой песне.
Последний день работы мартеновского цеха Выксунского металлургического завода
Смена уклада
Ударом по мартену стало развитие новых технологий получения стали во второй половине XX века.
Во-первых, технический прогресс позволил получать в промышленных масштабах чистый кислород, что сразу перевернуло соотношение сил между мартеном и конвертерами. Первые эксперименты с применением чистого кислорода для плавки были проведены еще в 1933–1936 годах в Киеве под руководством инженера Николая Мозгового. А с 1952 года технология стала использоваться в массовом промышленном производстве на заводах австрийской металлургической компании VOEST. Собственно, технология использования кислородных конвертеров известна также под альтернативным именем «процесс Линц—Донавитц», в честь двух австрийских городов, где впервые были построены промышленные кислородные конвертеры.
Кислородный конвертер позволял получать сталь в десять раз быстрее мартена, он отличается гораздо более высокой энергоэффективностью (мартеновская печь требует внешнего обогрева в течение всей плавки, конвертер разогревается сам). А использование чистого кислорода позволило избавиться от давней «болезни» бессемеровского и томасовского процессов — дополнительных примесей в стали и возможности плавить только чугун (кислородному конвертеру за счет более высокой окислительной способности чистого кислорода по зубам и смесь чугуна с ломом).
Вторым фактором против мартена стало развитие электрометаллургии. Первые экспериментальные электродуговые печи были построены еще в 1870-х годах. По иронии судьбы патент на электродуговую печь получил все тот же Карл Сименс — фактический изобретатель мартеновской печи. В 1907 году под руководством французского инженера Поля Эру был построен первый электрометаллургический завод в США. Если конвертер требует преимущественно чугуна, то электродуговая печь может взять на себя переплавку «излишков» лома. Долгое время распространение технологии упиралось в ограничение мощностей электрогенерации. Но во второй половине XX века мир увидел как взрывной рост электроэнергетики, так и совершенствование самой технологии электрометаллургии. Если в 1965 году электродуговая печь на тонну стали требовала 630 киловатт электроэнергии и 6,5 килограмма электродов, то к 1990-м этот показатель опустился до 350 киловатт и 2,2 килограмма.
Наконец, третьим технологическим аргументом против мартена стало распространение во второй половине XX века машин непрерывного литья заготовки (МНЛЗ). В 1952 году был выдан первый патент на машину подобного типа, к 1970-м МНЛЗ получили широчайшее распространение в металлургии развитых стран, а затем стали непременным атрибутом мировой металлургии вообще. И с мартеном, из-за специфики его плавки, МНЛЗ оказалась довольно плохо совместима.
И с 1970-х строить новые мартеновские печи в мире прекратили.
«Во второй половине XX века, с появлением мощных электродуговых печей и установок внепечной обработки стали с электроподогревом жидкой стали с последующим вакуумированием или продувкой инертными газами, а также с появлением широкой возможности автоматизации электропечей и установок внепечной металлургии, производство сталей получает новый виток и выходит на более качественный уровень по содержанию вредных примесей и газов. Таким образом, общая совокупность развития конвертерной и электростали, а также быстрота получения больших объемов жидкой стали и автоматизации процессов производства вытеснила мартеновское производство в большинстве стран мира», — говорит Анатолий Куликов.
Действительно, по данным Мировой ассоциации производителей стали (WSA), объем производства мартеновской стали в мире сократился с 195,4 млн тонн в 1974 году до 6,8 млн тонн в 2016-м. Доля мартеновского производства в общем объеме мировой выплавки стали за тот же временной период сократилась с 30% менее чем до 0,5%.
Ранее столь же обвальное падение наблюдалось при уходе мировой металлургии от бессемеровского процесса.
Снижение роли мартеновского производства наблюдалось и в нашей стране. Если в 1974 году на мартены пришлось 67% всей советской стали, то в 1990-м — чуть более 51%.
В Советском Союзе поднимался вопрос о возможности физического прекращения мартеновского производства. Но, как следует из выкладок советских экономистов, перепрофилирование средних размеров металлургического предприятия с мартенов на конвертеры стоило бы порядка 100–110 млн рублей в ценах конца 1970-х годов. И в условиях довольно наплевательского отношения к окружающей среде и планово дешевых энергоносителей это сочли нецелесообразным.
Загрузка металлургических мощностей в мире
Рынок решил
Ситуация принципиально изменилась с переходом экономики России на рыночные рельсы и повышением внимания к экологии. Часть печей была остановлена из экономических соображений. В ряде случаев за невидимой рукой рынка явно маячила тень правительства. Так, в 2013 году Минпромторг стал настаивать на выводе из эксплуатации всех мартеновских печей еще до конца 2015 года. «На мартеновское производство в 2013 году в России приходилось 28 процентов промышленных выбросов в атмосферу и свыше шести процентов сброса сточных вод», — говорил замминистра Глеб Никитин. В качестве альтернативы министерство предлагало строить электропечи.
Например, «Северсталь» полностью отказалась от мартеновских печей (а их в Череповце было 12!) в 2011 году, ММК — в 2003 году, «Евраз» - в 2006-м.
«Если сравнивать затраты на производство стали в мартене или, скажем, в дуговой печи, то при прочих равных затраты будут одного порядка, — говорит Дмитрий Чернышев. — Но за счет большего числа переделов и несовершенного способа разливки мартеновский способ по эффективности уступает электросталеплавильному. Это “отступление” мы наблюдали последние годы в мировой металлургии. Мы также понимали, что мартеновский способ морально устарел, что он вреден для экологии, поэтому давно ждали возможности уйти от его использования».
Как отмечают в компании, инвестиции в строительство собственных дополнительных сталеплавильных мощностей в Выксе для производства колес экономически неоправданны (у ВМЗ есть литейно-прокатный комплекс по выпуску горячекатаного проката мощностью 1,2 млн тонн, вся продукция которого перерабатывается в трубы среднего и малого диаметра).
«В течение нескольких лет мы искали внешнего поставщика стали. И как только был найден надежный партнер, мы приняли долгожданное решение об остановке мартена, — рассказывает Дмитрий Чернышев. — Таким образом, двигаясь в русле курса России на ужесточение природоохранных требований, мы решили наболевший экологический вопрос в Выксе, а параллельно и проблему использования устаревших технологий разливки в изложницы: необходимость соответствовать определенным требованиям накладывала непреодолимые ограничения на применение мартеновской стали для выпуска некоторой колесной продукции».
Отметим, что в общей сложности в России объем производства мартеновской стали упал с 33,5 млн тонн в 1992 году до 1,6 млн тонн в 2016-м. Доля мартена в общенациональной выплавке стали за тот же период сократилась с 50 до 2,4%. То есть все самое главное уже произошло — закрытие выксунского мартена лишь ставит точку в уже свершившемся переходе.
Теперь практически все мировое мартеновское производство оказывается сосредоточено на Украине, которая все больше превращается в заповедник архаичных технологий.
После мартена
Колесопрокатное производство ВМЗ после закрытия мартена перейдет на сталь сторонних поставщиков. В начале 2017 года ОМК уже заключила долгосрочный (на десять лет) контракт с «Уральской сталью».
«В партнеры по обеспечению колесного производства сталью был выбран завод “Уральская сталь” из города Новотроицка Оренбургской области, — рассказывает руководитель коммерческого департамента ОМК Эдуард Степанцов. — Потребность в сырье колесопрокатного производства ВМЗ при полной загрузке составляет около 400 тысяч тонн стали в год».
Эдуард Степанцов уверяет, что закрытие мартена в Выксе не приведет к перебоям в поставках железнодорожных колес. Общие производственные мощности производителей в Евразийском экономическом союзе на 2018 год составляют порядка 1,5 млн штук в год, в том числе 850 тыс. — у ВМЗ. По оценке ОМК, основанной на производстве вагонов в 2017 году, заявлениях вагоностроителей и статистике потребления, максимальная потребность в колесах на рынке Союза в 2018-2019 годах может составить не более 1,47 млн штук в год. Поэтому существующие внутренние мощности способны полностью удовлетворить потребности в колесах. Не пострадает и качество продукции.
«Сегодня иная ситуация. Независимо от того, каким способом идет производство стали, ее качество, если говорить упрощенно, достигается исходным сырьем и путем так называемого доведения по химическому составу — ее дополнительной обработкой вне печи, — рассказывает Дмитрий Чернышев. — Сталеплавильный цех ВМЗ в составе мартеновской печи и современного комплекса внепечной обработки стали — печи–ковша и вакууматора, введенных в строй в 2005 году, был способен производить сталь в полном соответствии с требованиями по качеству. Но лучшая альтернатива мартену, вне сомнения, современное электросталеплавильное производство».
Перед мировой металлургической отраслью сохраняется проблема неполной загрузки мощностей (см. график 4). Более того, конкуренция производителей может обостряться за счет того, что с распространением альтернативных конструкционных материалов сжимается потенциальный рынок для стали. Например, содержание стали в автомобиле сократилось с 86% по массе в 1980-х до 66% в 2000-х и продолжает снижаться. Даже рост мировой экономики все слабее коррелирует с динамикой стального рынка (см. график 5).
Ответом на эти вызовы может быть все возрастающее внимание к технологичности производства. В частности, Анатолий Куликов полагает, что в перспективе можно ожидать еще одного технологического перехода в отрасли: «Открытие мини-заводов на основе высокопроизводительных электропечей представляет более широкие возможности, чем конвертерное производство. Уже сейчас время расплавления и массы плавок конвертеров и электропечей сопоставимы. Производство электростали с использованием технологий вторичной металлургии более мобильно и экологично по сравнению с конвертерным производством, а уровень автоматизации получения электростали находится на высоком уровне».
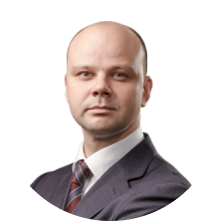
Читайте еще