Бережливое производство в действии
12.01.2018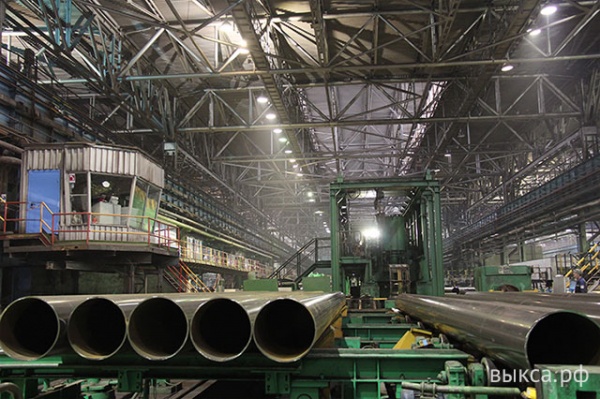
В начале декабря 2017 г. Выксунский металлургический завод (ВМЗ), входящий в Объединенную металлургическую компанию (ОМК), по итогам аудита японской компании Toyota Engineering Corporation (ТЕС) получил серебряную медаль за высокий уровень организации производственной системы (ПС).
ВМЗ удостоился наивысшей оценки среди всех мировых металлургических компаний и среди российских компаний всех отраслей, внедряющих производственную систему. К этому результату ВМЗ следовал шесть лет, в течение которых на заводе произошла настоящая революция в управлении и организации труда.
Для чего это нужно?
Конкурентоспособность — это то, что рождается внутри компании. Сегодня все ведущие производители на мировом рынке работают примерно в одинаковых условиях. Многие крупные компании могут позволить себе самое эффективное и производительное оборудование, отметила на практической конференции «Опыт развития эффективных производственных систем в России», проходившей в Выксе (Нижегородская обл.) 5-6 декабря 2017 г., председатель правления ОМК Н. Еремина. Ни у кого нет значимых преимуществ перед конкурентами ни в стоимости приобретаемого сырья, ни в отпускных ценах на готовую продукцию. Поэтому выигрывает тот, кто добьется наилучших результатов в организации труда, в снижении потерь, в поиске и использовании внутренних резервов, в обеспечении стабильно высокого уровня качества.
Каждая компания решает эти вопросы по-своему, однако многие изучают и перенимают опыт успешных коллег. Сегодня законодателями мод в управлении производством считаются японцы, точнее, корпорация Toyota, за полвека прошедшая путь от небольшого автопроизводителя в бедной послевоенной Японии до ведущего автомобилестроителя в мире.
Производственная система Toyota, возникшая в 1950-1960-е годы, направлена прежде всего на снижение себестоимости и повышение прибыльности бизнеса. Оказалось, что путь к высоким финансовым показателям лежит через устойчиво высокое качество, чтобы не приходилось тратить время и средства на исправление ошибок и переделки, а также через минимизацию, а лучше ликвидацию потерь ресурсов, времени, денег, трудовых усилий.
Для достижения этих целей потребовалось задействовать в первую очередь человеческий фактор. Наиболее эффективная борьба с излишними, ненужными затратами велась посредством небольших, но частых и непрерывных улучшений непосредственно на рабочих местах. Но, чтобы добиться таких результатов, необходимо было активно вовлекать сотрудников в дела компании — поощрять (и материальными, и нематериальными методами) их инициативность, рушить административные и социальные перегородки, обучать персонал и наделять его ответственностью.
Так одно цеплялось за другое, и в итоге у Toyota сформировалась особая система менеджмента, получившая международное признание в начале 1990-х годов. В 1984 г. японская компания, стремясь проникнуть на американский рынок и обойти выстраиваемые там протекционистские барьеры, основала совместное предприятие с General Motors и взяла под свое управление завод NUMM в Калифорнии, остановленный в 1982 г. из-за хронических убытков и падения качества. Японцы заново запустили его, внедрили на нем свою систему и превратили его в лучшее автомобилестроительное предприятие в Америке.
Таким поворотом заинтересовались в Массачусетском технологическом институте — наиболее известном и уважаемом техническом учебном заведении в США. Его специалисты несколько лет изучали опыт Toyota, а в 1990 г. опубликовали книгу «Машина, которая изменила мир», ставшую бестселлером и познакомившую с этим опытом весь мир.
Освоить передовые методы захотелось многим. В структуре японской корпорации даже создали консалтинговое подразделение Toyota Engineering Corporation, которое занимается внедрением этих методик по всему миру. Сейчас в нем работает около 70 консультантов — бывших менеджеров Toyota Motors и других компаний группы. Сегодня Toyota представляет собой весьма диверсифицированный концерн, в который входят даже металлургические заводы, что позволяет применять инструменты бережливого производства в различных отраслях. На конференции «Опыт развития эффективных производственных систем в России» выступали, например, представители пищевой промышленности, приборостроения и даже медицины.
На Выксунском металлургическом заводе создание адаптированной производственной системы, как рассказал управляющий директор предприятия А. Барыков, началось в 2011 г. Оно имело четкие цели — активизация темпов роста и снижение потерь. До этого у завода уже был опыт внедрения передовых управленческих технологий. В 2002—2003 гг. совместно с известной консалтинговой компанией McKinsey была реализована программа оптимизации производства, а в 2010 г. — программа по повышению культуры безопасности труда. Собственно, и в 2011 г. концепцию развития производственной системы в группе ОМК разработали с помощью консультантов McKinsey. Они же помогли сформировать команду по ее внедрению.
В 2015 г. ВМЗ впервые прошел аудит TEC и по его итогам получил 2,65 балла по пятибалльной системе. И это не тройка с минусом, а весьма высокий результат, сравнимый с показателями японских металлургических компаний. В 2016 г. завод наработал на «бронзовый» уровень 3,11 балла, а по итогам аудита 2017 г. получил 3,54 балла, и это наилучший результат в мировой металлургической отрасли. Как отметил президент ТЕС Тосихиро Ямада (Toshihiro Yamada), такого быстрого прогресса не демонстрировало на его памяти ни одно предприятие. Кроме того, ВМЗ стал первой «серебряной» компанией в России. Кстати, освоением системы гибкого производства занимаются в нашей стране уже несколько десятков предприятий, в том числе другие заводы группы ОМК. Один из них, Альметьевский трубный завод, по предварительным оценкам, показал уровень зрелости ПС, соответствующий бронзовой медали TEC.
Безусловно, награда не самоцель. По словам А. Барыкова, внедрение производственной системы на ВМЗ стало основой развития предприятия, позволяющей достигать амбициозных целей.
Как это создавалось?
По словам консультанта TEC Тацуми Кимуры (Tatsumi Kimura), непосредственно работающего в качестве аудитора с ВМЗ, производственная система внедряется в двух направлениях — сверху вниз и снизу вверх. Но стартовать процесс должен сверху. У компании должен быть лидер, который подает личный пример и создает благоприятную среду для улучшений и пробуждения инициативности сотрудников. На предприятии следует создать атмосферу, способствующую переменам и терпимую к ошибкам. Если что-то не удалось, гласит один из принципов Toyota, нужно усвоить урок и работать над новыми изменениями.
Начинать любое дело трудно. Внедрение новой производственной системы на ВМЗ в 2011 г. стартовало в обстановке всеобщего скептицизма. На первых порах многое не получалось. И, как рассказывает О. Захаров, начальник управления по развитию производственной системы на ВМЗ, что-то сдвинулось, когда руководство предприятия стало задавать себе вопросы о сопутствующих успеха.
Ключевых факторов оказалось три. Во-первых, это человек, который нагрузит все на себя и потащит. Таким лидером на ВМЗ стал управляющий директор. Большую роль во внедрении ПС сыграли его обходы производственных участков, которые сегодня стали ежедневными. Таким образом решаются сразу несколько важных задач. Например, руководитель может напрямую, из первых рук, получить информацию о текущем состоянии различных подразделений, об их проблемах и решениях. Создавалась мощная обратная связь между топ-менеджментом и оперативным звеном. Директор не только оценивает, как на местах внедряется система бережливого производства, но и обучает людей, помогает распространению наилучших практик.
Сейчас на ВМЗ такие обходы осуществляют практически все руководители. Начальники цехов бывают, как говорится, в гостях друг у друга, что позволяет сделать оценку незамыленным взглядом. Таким образом обеспечивается вовлеченность руководящего состава в повседневный процесс улучшений и создается второй ключевой фактор — команда, которая будет помогать лидеру в распространении и реализации принципов бережливого производства.
Третий фактор, на который также необходимо обратить внимание, — это идеология и четкое целеполагание. Нужно понимать, что компания хочет сделать и что желает получить на выходе. Прежде чем новые приемы и методы работы станут привычной средой для персонала компании, людей необходимо обучать работе в новых условиях, а иногда и подталкивать к этому.
В соответствии с концепцией ПС ОМК производственная система ВМЗ имеет три основных элемента. Первый из них — активная среда. Иными словами, это люди, которые занимаются улучшениями на своих рабочих местах, — неравнодушный коллектив, готовый не только принять изменения, но и инициировать их. Как говорилось на конференции, правильный ответ на вопрос: «Кто отвечает за развитие производственной системы?», заданный любому сотруднику компании, звучит так: «За это отвечаю я!».
Как показали аудиты, проведенные TEC на Выксунском металлургическом заводе, еще в 2015 г. деятельность руководства предприятия получила высокую оценку. В чем-то его топ-менеджеры даже превосходили коллег из Toyota Motors. Но вот действенного механизма управления снизу вверх тогда еще не существовало, он создан в последние два года. И немалой заслугой управленцев ВМЗ стало то, что им удалось расшевелить коллектив предприятия, приобщить его к решению реальных проблем и стимулировать его рационализаторскую энергию.
Процесс создания такого коллектива, как уже отмечалось, начинается с лидера и команды его соратников, которые готовы показать личный пример. Они должны запустить систему, найти и привлечь первых инициаторов, поручить им реальные дела, открыто поощрить их за достигнутые результаты, обеспечить максимальную огласку и поддержку, продемонстрировать всем, что это не показуха и не краткосрочная кампания, а новый образ жизни.
По мнению японских консультантов, в идеале в процесс непрерывных улучшений должно быть вовлечено 80—90% персонала, но и оставшихся надо пытаться расшевелить, привлечь к общему делу. У российских участников конференции на этот счет возникли сомнения. Руководитель одной из компаний прямо сказал, что принимает на работу только тех, кто находится на одной волне с коллективом и готов воспринять общие ценности. Но подобный подход применим к сравнительно небольшому предприятию, где трудится немногим более сотни человек. Для такого громадного завода, как ВМЗ, где работает 15 тыс. сотрудников, это не вариант. Там необходимо работать со всеми.
Поэтому людей надо учить, информировать, доводить до каждого, что перемены происходят в интересах и компании в целом, и ее сотрудников. Для распространения идеологии и обучения инструментам бережливого производства на ВМЗ была создана Академия ПС, в которой прошли обучение более 4 тыс. человек. При этом в качестве преподавателей выступают как рабочие, имеющие положительный опыт внедрения инструментов ПС, так и руководство завода, включая управляющего директора. Все без исключения сотрудники предприятия регулярно проходят курсы на рабочих местах, которые на ВМЗ на 80—90% компьютеризированы, даже в цехах. Для того чтобы совершенствовать процесс обучения и снизить время на его организацию, разработали специальную программу, интегрированную с обучающим модулем ERP-системы.
Важную роль, по словам О. Захарова, сыграли публичные защиты личных презентаций руководителей всех уровней — от управляющего директора до старших мастеров. И это не формальные годовые планы личностного роста, а конкретные обязательства, за которые каждый несет ответственность перед коллективом и компанией.
При этом поощряются и поддерживаются амбициозные планы, сулящие значительные прорывы на каких-либо направлениях. Все они размещены в свободном доступе на веб-сайте компании и непосредственно на стендах визуализации в подразделениях.
Чтобы объединить многотысячный коллектив завода в команду, необходимы и эффективные каналы внутренних коммуникаций — инструмент обратной связи и общения руководителей с подчиненными. Такую роль играет интранет-портал производственной системы ВМЗ. У него высокий уровень оперативности. Так, по итогам обхода директором какого-либо производственного участка уже через 3-4 часа на портале появляется достаточно подробный отчет, в котором отражены позитивные и негативные моменты. Каждый сотрудник может дать анонимный комментарий — запрещается только ненормативная лексика и, так сказать, переход на личности. Некоторые статьи/новости собирают по несколько десятков, а то и сотни комментариев, и в них встречаются интересные идеи.
Второй основной элемент производственной системы ВМЗ — стандартизация. Лучшие практики формализуются в виде рабочих стандартов — карт пошагового выполнения операций и стандартных операционных процедур для каждого рабочего места, для каждой операции. Причем составляют эти документы группы сотрудников, в которые входят и сами рабочие, которые, можно сказать, пишут их для себя. Такие правила не воспринимаются как нечто навязанное со стороны. Контроль за соблюдением правил трехуровневый — его осуществляют сменные мастера, технологи и ОТК, а также регулярно проводится аудит.
Команда, написавшая стандарт, потом совершенствует его, а также учит по нему новичков. Данная унификация позволила изменить процесс вливания в коллектив новых сотрудников. Ранее они прикреплялись к опытным рабочим-наставникам, теперь учить может вся бригада. Каждый через свой личный кабинет в обучающем модуле ERP-системы проходит непосредственно на рабочем месте учебные курсы. Сдав тесты, он получает нужные допуски.
Внедрению новых стандартов и правил помогает визуализация. В каждом цехе проведена разметка, стандарты и правила изложены в наглядном виде на стендах. Рабочее пространство оптимизировано, чтобы все необходимое для работы — инструмент, оснастка, материалы, стандарты — находилось под рукой и в нужном количестве. В последние годы на ВМЗ начали внедрять систему бережливого производства и в офисах, премируя сотрудников за самые оптимально организованные кабинеты. Как отметил О. Захаров, много на этом не заработаешь, но наведение порядка в административных подразделениях должно показать рабочим, занятым в цехах, что производственная система распространяется на всех. Упорядоченность влияет на сотрудников, настраивая их на рабочий лад. Да и трудиться, когда вокруг все рационально организовано, комфортнее и удобнее.
Третий ключевой элемент производственной системы — «идеальный поток». В основе этого направления лежит применение инструментов ПС с целью выстраивания процесса создания ценности с минимальными потерями и удовлетворяющим потребителя качеством. Система отчетности должна быть эффективна, прозрачна и достоверна, для достижения чего используются механизмы автоматизации получения данных.
Как это работает?
Началом преобразований на заводе стала реализация проектов повышения эффективности производственных участков и функций. С того момента реализовано более 50 проектов с совокупным экономическим эффектом 2,5 млрд. руб. Далее они трансформировались в проекты по совершенствованию отдельных операций. Один из показательных примеров — проекты по сокращению времени переналадок оборудования в цехах по методике SMED (Single Minute Exchange Die). Для этого создавались кросс-функциональные рабочие группы, которые изучали проблемы, искали узкие места, подавали предложения по их устранению. Результаты оказались весьма впечатляющими. За два года длительность переналадок в основных цехах ВМЗ сократилась на 55%, что дало экономический эффект 300 млн. руб., позволило повысить гибкость производства, плюс у завода появилась возможность браться за сравнительно небольшие заказы, число которых в последнее время увеличивается. Причем достигнуто это было без каких-либо крупных капиталовложений, только за счет лучшей организации труда и благодаря усилиям сотрудников, выполняющих основные операции.
Еще одно направление развития — оптимизация работы транспорта. Средняя продолжительность погрузки машины с августа 2013 г. по январь 2014 г. сократилась с 17 до 4 часов. А в другом «кейсе» временные затраты на подготовку комплекта сопроводительной документации при отправке труб по железной дороге уменьшились с 20,5 часа в сентябре 2015 г. до 3,8 часа в сентябре 2016 г. И таких примеров десятки, если не сотни.
Система непрерывных улучшений позволила достичь высокого уровня вовлеченности персонала в процесс развития. Сегодня сотрудники завода подают около 2 тыс. предложений по улучшениям в месяц, что в 2017 г. принесло эффект около 200 млн. руб. За последние годы ВМЗ добился существенного повышения качества продукции, что помогло ОМК усилить позиции на российском и мировом рынке сварных труб, в частности, в нефтегазовом сегменте.
Основная работа по непрерывным улучшениям ведется на ВМЗ в МИГах (малые инициативные группы) — такую аббревиатуру, совпадающую с названием известного самолета, придумали на заводе для обозначения японских кружков качества. В начале декабря 2017 г. на предприятии насчитывалось более 310 малых инициативных групп, в работе которых участвует свыше 1,9 тыс. сотрудников. Всего в МИГах реализовано к настоящему времени около 900 проектов, свыше 320 находится в работе. Благодаря их деятельности завод получил прямой финансовый выигрыш более 80 млн. руб., не считая косвенного воздействия.
Д. Махров, директор ВМЗ по качеству, рассказал подробнее, что такое МИГ. Это добровольная группа из 3—9 человек (чаще всего 4—6), работающих на одном производственном участке и решающих какую-либо проблему, непосредственно влияющую на производственные процессы. Группы формируют графики еженедельных встреч, на которых происходит поиск первопричин и вырабатываются мероприятия по их устранению.
На японских предприятиях такие кружки качества — привычный инструмент, существующий десятилетия. На ВМЗ их пришлось создавать с нуля. Первым этапом стало определение лидеров. В чем-то эту задачу решало руководство, подыскивая авторитетных сотрудников, которым поручали определенные задания, потом люди начали сами выдвигаться, проявлять инициативу, раз она поддерживается и поощряется. Из практики первых групп родился стандарт по деятельности МИГов, на который могли опираться новые малые коллективы. Затем лидеров МИГов учили в Академии ПС искать и выявлять проблемы, анализировать, вести мозговой штурм, управлять членами групп.
Рабочие зачастую находили решение достаточно сложных проблем, до которых могли просто не дойти руки у руководства. Например, одна из групп занялась проблемой, возникшей при резке слябов. Два резака работали не совсем соосно, из-за чего слябы приходилось дорабатывать вручную, теряя время и ресурсы. Члены МИГа выявили проблему и привлекли специалистов к ее решению. В результате отремонтировали несколько узлов, на других провели регламентные работы, улучшили программное обеспечение. В результате повысилось качество резки и значительно снизился расход кислорода и природного газа.
Другой случай — в центральной заводской лаборатории дирекции по качеству обратили внимание на высокую долю неудовлетворительных результатов испытаний из-за разрушения образцов. Создали инициативную группу. Проект оказался весьма сложным, этап диагностики и выявления первопричин проблем длился более пяти месяцев. Была сформирована программа мероприятий, в которую вошло в том числе изучение передового опыта других предприятий. Привлекли специалистов для разработки и внедрения новых стандартов отбора образцов, автоматизировали процессы, для того чтобы снизить влияние человеческого фактора, модернизировали оборудование. В итоге процент брака при проведении данных испытаний сократился почти в 8 раз, что значительно превысило изначальное задание.
По словам Д. Махрова, данные случаи показали людям, что они реально могут что-то сделать. Это помогло продвинуть дальше идею с МИГами и повысить уровень вовлеченности персонала. На сегодняшний день участниками малых инициативных группы на предприятии являются около 20% сотрудников, но руководство ВМЗ надеется довести долю до 50%. Чтобы продвинуть идею, на заводе ежеквартально с 2016 г. проводятся конкурсы на лучший проект МИГов с призовым фондом 1,5 млн. руб.
Как отмечает президент ТЕС Тосихиро Ямада, топ-менеджеры компаний часто уделяют основное внимание достижению благоприятных показателей — доходу, прибыли, рентабельности, отношению долга к EBTDA. Однако система бережливого производства, по его словам, помогает оптимизировать использование внутренних ресурсов — персонала, технологий, оборудования, системы организации труда. И, как показывает опыт мирового бизнеса, благодаря высокой эффективности на этих направлениях, личностному развитию сотрудников, стабильно высокому качеству обеспечиваются хорошие финансовые результаты. В целом все участники конференции «Опыт развития эффективных производственных систем в России» отметили очевидные успехи в развитии компаний, выбравших путь внедрения инструментов бережливого производства.
***
ВМЗ стал первой «серебряной» компанией в России. Кстати, освоением системы бережливого производства занимаются в нашей стране уже несколько десятков предприятий, в том числе другие заводы группы ОМК.
Как показали аудиты, проведенные TEC на Выксунском металлургическом заводе, еще в 2015 г. деятельность руководства предприятия получила высокую оценку.
На Выксунском металлургическом заводе создание адаптированной производственной системы, как рассказал управляющий директор предприятия А. Барыков, началось в 2011 г. Оно имело четкие цели — активизация темпов роста и снижение потерь.
Лучшие практики формализуются в виде рабочих стандартов — карт пошагового выполнения операций и стандартных операционных процедур для каждого рабочего места, для каждой операции. Причем составляют эти документы группы сотрудников, в которые входят и сами рабочие, которые, можно сказать, пишут их для себя.
Началом преобразований на заводе стала реализация проектов повышения эффективности производственных участков и функций. С того момента реализовано более 50 проектов с экономическим эффектом
ВМЗ удостоился наивысшей оценки среди всех мировых металлургических компаний и среди российских компаний всех отраслей, внедряющих производственную систему. К этому результату ВМЗ следовал шесть лет, в течение которых на заводе произошла настоящая революция в управлении и организации труда.
Для чего это нужно?
Конкурентоспособность — это то, что рождается внутри компании. Сегодня все ведущие производители на мировом рынке работают примерно в одинаковых условиях. Многие крупные компании могут позволить себе самое эффективное и производительное оборудование, отметила на практической конференции «Опыт развития эффективных производственных систем в России», проходившей в Выксе (Нижегородская обл.) 5-6 декабря 2017 г., председатель правления ОМК Н. Еремина. Ни у кого нет значимых преимуществ перед конкурентами ни в стоимости приобретаемого сырья, ни в отпускных ценах на готовую продукцию. Поэтому выигрывает тот, кто добьется наилучших результатов в организации труда, в снижении потерь, в поиске и использовании внутренних резервов, в обеспечении стабильно высокого уровня качества.
Каждая компания решает эти вопросы по-своему, однако многие изучают и перенимают опыт успешных коллег. Сегодня законодателями мод в управлении производством считаются японцы, точнее, корпорация Toyota, за полвека прошедшая путь от небольшого автопроизводителя в бедной послевоенной Японии до ведущего автомобилестроителя в мире.
Производственная система Toyota, возникшая в 1950-1960-е годы, направлена прежде всего на снижение себестоимости и повышение прибыльности бизнеса. Оказалось, что путь к высоким финансовым показателям лежит через устойчиво высокое качество, чтобы не приходилось тратить время и средства на исправление ошибок и переделки, а также через минимизацию, а лучше ликвидацию потерь ресурсов, времени, денег, трудовых усилий.
Для достижения этих целей потребовалось задействовать в первую очередь человеческий фактор. Наиболее эффективная борьба с излишними, ненужными затратами велась посредством небольших, но частых и непрерывных улучшений непосредственно на рабочих местах. Но, чтобы добиться таких результатов, необходимо было активно вовлекать сотрудников в дела компании — поощрять (и материальными, и нематериальными методами) их инициативность, рушить административные и социальные перегородки, обучать персонал и наделять его ответственностью.
Так одно цеплялось за другое, и в итоге у Toyota сформировалась особая система менеджмента, получившая международное признание в начале 1990-х годов. В 1984 г. японская компания, стремясь проникнуть на американский рынок и обойти выстраиваемые там протекционистские барьеры, основала совместное предприятие с General Motors и взяла под свое управление завод NUMM в Калифорнии, остановленный в 1982 г. из-за хронических убытков и падения качества. Японцы заново запустили его, внедрили на нем свою систему и превратили его в лучшее автомобилестроительное предприятие в Америке.
Таким поворотом заинтересовались в Массачусетском технологическом институте — наиболее известном и уважаемом техническом учебном заведении в США. Его специалисты несколько лет изучали опыт Toyota, а в 1990 г. опубликовали книгу «Машина, которая изменила мир», ставшую бестселлером и познакомившую с этим опытом весь мир.
Освоить передовые методы захотелось многим. В структуре японской корпорации даже создали консалтинговое подразделение Toyota Engineering Corporation, которое занимается внедрением этих методик по всему миру. Сейчас в нем работает около 70 консультантов — бывших менеджеров Toyota Motors и других компаний группы. Сегодня Toyota представляет собой весьма диверсифицированный концерн, в который входят даже металлургические заводы, что позволяет применять инструменты бережливого производства в различных отраслях. На конференции «Опыт развития эффективных производственных систем в России» выступали, например, представители пищевой промышленности, приборостроения и даже медицины.
На Выксунском металлургическом заводе создание адаптированной производственной системы, как рассказал управляющий директор предприятия А. Барыков, началось в 2011 г. Оно имело четкие цели — активизация темпов роста и снижение потерь. До этого у завода уже был опыт внедрения передовых управленческих технологий. В 2002—2003 гг. совместно с известной консалтинговой компанией McKinsey была реализована программа оптимизации производства, а в 2010 г. — программа по повышению культуры безопасности труда. Собственно, и в 2011 г. концепцию развития производственной системы в группе ОМК разработали с помощью консультантов McKinsey. Они же помогли сформировать команду по ее внедрению.
В 2015 г. ВМЗ впервые прошел аудит TEC и по его итогам получил 2,65 балла по пятибалльной системе. И это не тройка с минусом, а весьма высокий результат, сравнимый с показателями японских металлургических компаний. В 2016 г. завод наработал на «бронзовый» уровень 3,11 балла, а по итогам аудита 2017 г. получил 3,54 балла, и это наилучший результат в мировой металлургической отрасли. Как отметил президент ТЕС Тосихиро Ямада (Toshihiro Yamada), такого быстрого прогресса не демонстрировало на его памяти ни одно предприятие. Кроме того, ВМЗ стал первой «серебряной» компанией в России. Кстати, освоением системы гибкого производства занимаются в нашей стране уже несколько десятков предприятий, в том числе другие заводы группы ОМК. Один из них, Альметьевский трубный завод, по предварительным оценкам, показал уровень зрелости ПС, соответствующий бронзовой медали TEC.
Безусловно, награда не самоцель. По словам А. Барыкова, внедрение производственной системы на ВМЗ стало основой развития предприятия, позволяющей достигать амбициозных целей.
Как это создавалось?
По словам консультанта TEC Тацуми Кимуры (Tatsumi Kimura), непосредственно работающего в качестве аудитора с ВМЗ, производственная система внедряется в двух направлениях — сверху вниз и снизу вверх. Но стартовать процесс должен сверху. У компании должен быть лидер, который подает личный пример и создает благоприятную среду для улучшений и пробуждения инициативности сотрудников. На предприятии следует создать атмосферу, способствующую переменам и терпимую к ошибкам. Если что-то не удалось, гласит один из принципов Toyota, нужно усвоить урок и работать над новыми изменениями.
Начинать любое дело трудно. Внедрение новой производственной системы на ВМЗ в 2011 г. стартовало в обстановке всеобщего скептицизма. На первых порах многое не получалось. И, как рассказывает О. Захаров, начальник управления по развитию производственной системы на ВМЗ, что-то сдвинулось, когда руководство предприятия стало задавать себе вопросы о сопутствующих успеха.
Ключевых факторов оказалось три. Во-первых, это человек, который нагрузит все на себя и потащит. Таким лидером на ВМЗ стал управляющий директор. Большую роль во внедрении ПС сыграли его обходы производственных участков, которые сегодня стали ежедневными. Таким образом решаются сразу несколько важных задач. Например, руководитель может напрямую, из первых рук, получить информацию о текущем состоянии различных подразделений, об их проблемах и решениях. Создавалась мощная обратная связь между топ-менеджментом и оперативным звеном. Директор не только оценивает, как на местах внедряется система бережливого производства, но и обучает людей, помогает распространению наилучших практик.
Сейчас на ВМЗ такие обходы осуществляют практически все руководители. Начальники цехов бывают, как говорится, в гостях друг у друга, что позволяет сделать оценку незамыленным взглядом. Таким образом обеспечивается вовлеченность руководящего состава в повседневный процесс улучшений и создается второй ключевой фактор — команда, которая будет помогать лидеру в распространении и реализации принципов бережливого производства.
Третий фактор, на который также необходимо обратить внимание, — это идеология и четкое целеполагание. Нужно понимать, что компания хочет сделать и что желает получить на выходе. Прежде чем новые приемы и методы работы станут привычной средой для персонала компании, людей необходимо обучать работе в новых условиях, а иногда и подталкивать к этому.
В соответствии с концепцией ПС ОМК производственная система ВМЗ имеет три основных элемента. Первый из них — активная среда. Иными словами, это люди, которые занимаются улучшениями на своих рабочих местах, — неравнодушный коллектив, готовый не только принять изменения, но и инициировать их. Как говорилось на конференции, правильный ответ на вопрос: «Кто отвечает за развитие производственной системы?», заданный любому сотруднику компании, звучит так: «За это отвечаю я!».
Как показали аудиты, проведенные TEC на Выксунском металлургическом заводе, еще в 2015 г. деятельность руководства предприятия получила высокую оценку. В чем-то его топ-менеджеры даже превосходили коллег из Toyota Motors. Но вот действенного механизма управления снизу вверх тогда еще не существовало, он создан в последние два года. И немалой заслугой управленцев ВМЗ стало то, что им удалось расшевелить коллектив предприятия, приобщить его к решению реальных проблем и стимулировать его рационализаторскую энергию.
Процесс создания такого коллектива, как уже отмечалось, начинается с лидера и команды его соратников, которые готовы показать личный пример. Они должны запустить систему, найти и привлечь первых инициаторов, поручить им реальные дела, открыто поощрить их за достигнутые результаты, обеспечить максимальную огласку и поддержку, продемонстрировать всем, что это не показуха и не краткосрочная кампания, а новый образ жизни.
По мнению японских консультантов, в идеале в процесс непрерывных улучшений должно быть вовлечено 80—90% персонала, но и оставшихся надо пытаться расшевелить, привлечь к общему делу. У российских участников конференции на этот счет возникли сомнения. Руководитель одной из компаний прямо сказал, что принимает на работу только тех, кто находится на одной волне с коллективом и готов воспринять общие ценности. Но подобный подход применим к сравнительно небольшому предприятию, где трудится немногим более сотни человек. Для такого громадного завода, как ВМЗ, где работает 15 тыс. сотрудников, это не вариант. Там необходимо работать со всеми.
Поэтому людей надо учить, информировать, доводить до каждого, что перемены происходят в интересах и компании в целом, и ее сотрудников. Для распространения идеологии и обучения инструментам бережливого производства на ВМЗ была создана Академия ПС, в которой прошли обучение более 4 тыс. человек. При этом в качестве преподавателей выступают как рабочие, имеющие положительный опыт внедрения инструментов ПС, так и руководство завода, включая управляющего директора. Все без исключения сотрудники предприятия регулярно проходят курсы на рабочих местах, которые на ВМЗ на 80—90% компьютеризированы, даже в цехах. Для того чтобы совершенствовать процесс обучения и снизить время на его организацию, разработали специальную программу, интегрированную с обучающим модулем ERP-системы.
Важную роль, по словам О. Захарова, сыграли публичные защиты личных презентаций руководителей всех уровней — от управляющего директора до старших мастеров. И это не формальные годовые планы личностного роста, а конкретные обязательства, за которые каждый несет ответственность перед коллективом и компанией.
При этом поощряются и поддерживаются амбициозные планы, сулящие значительные прорывы на каких-либо направлениях. Все они размещены в свободном доступе на веб-сайте компании и непосредственно на стендах визуализации в подразделениях.
Чтобы объединить многотысячный коллектив завода в команду, необходимы и эффективные каналы внутренних коммуникаций — инструмент обратной связи и общения руководителей с подчиненными. Такую роль играет интранет-портал производственной системы ВМЗ. У него высокий уровень оперативности. Так, по итогам обхода директором какого-либо производственного участка уже через 3-4 часа на портале появляется достаточно подробный отчет, в котором отражены позитивные и негативные моменты. Каждый сотрудник может дать анонимный комментарий — запрещается только ненормативная лексика и, так сказать, переход на личности. Некоторые статьи/новости собирают по несколько десятков, а то и сотни комментариев, и в них встречаются интересные идеи.
Второй основной элемент производственной системы ВМЗ — стандартизация. Лучшие практики формализуются в виде рабочих стандартов — карт пошагового выполнения операций и стандартных операционных процедур для каждого рабочего места, для каждой операции. Причем составляют эти документы группы сотрудников, в которые входят и сами рабочие, которые, можно сказать, пишут их для себя. Такие правила не воспринимаются как нечто навязанное со стороны. Контроль за соблюдением правил трехуровневый — его осуществляют сменные мастера, технологи и ОТК, а также регулярно проводится аудит.
Команда, написавшая стандарт, потом совершенствует его, а также учит по нему новичков. Данная унификация позволила изменить процесс вливания в коллектив новых сотрудников. Ранее они прикреплялись к опытным рабочим-наставникам, теперь учить может вся бригада. Каждый через свой личный кабинет в обучающем модуле ERP-системы проходит непосредственно на рабочем месте учебные курсы. Сдав тесты, он получает нужные допуски.
Внедрению новых стандартов и правил помогает визуализация. В каждом цехе проведена разметка, стандарты и правила изложены в наглядном виде на стендах. Рабочее пространство оптимизировано, чтобы все необходимое для работы — инструмент, оснастка, материалы, стандарты — находилось под рукой и в нужном количестве. В последние годы на ВМЗ начали внедрять систему бережливого производства и в офисах, премируя сотрудников за самые оптимально организованные кабинеты. Как отметил О. Захаров, много на этом не заработаешь, но наведение порядка в административных подразделениях должно показать рабочим, занятым в цехах, что производственная система распространяется на всех. Упорядоченность влияет на сотрудников, настраивая их на рабочий лад. Да и трудиться, когда вокруг все рационально организовано, комфортнее и удобнее.
Третий ключевой элемент производственной системы — «идеальный поток». В основе этого направления лежит применение инструментов ПС с целью выстраивания процесса создания ценности с минимальными потерями и удовлетворяющим потребителя качеством. Система отчетности должна быть эффективна, прозрачна и достоверна, для достижения чего используются механизмы автоматизации получения данных.
Как это работает?
Началом преобразований на заводе стала реализация проектов повышения эффективности производственных участков и функций. С того момента реализовано более 50 проектов с совокупным экономическим эффектом 2,5 млрд. руб. Далее они трансформировались в проекты по совершенствованию отдельных операций. Один из показательных примеров — проекты по сокращению времени переналадок оборудования в цехах по методике SMED (Single Minute Exchange Die). Для этого создавались кросс-функциональные рабочие группы, которые изучали проблемы, искали узкие места, подавали предложения по их устранению. Результаты оказались весьма впечатляющими. За два года длительность переналадок в основных цехах ВМЗ сократилась на 55%, что дало экономический эффект 300 млн. руб., позволило повысить гибкость производства, плюс у завода появилась возможность браться за сравнительно небольшие заказы, число которых в последнее время увеличивается. Причем достигнуто это было без каких-либо крупных капиталовложений, только за счет лучшей организации труда и благодаря усилиям сотрудников, выполняющих основные операции.
Еще одно направление развития — оптимизация работы транспорта. Средняя продолжительность погрузки машины с августа 2013 г. по январь 2014 г. сократилась с 17 до 4 часов. А в другом «кейсе» временные затраты на подготовку комплекта сопроводительной документации при отправке труб по железной дороге уменьшились с 20,5 часа в сентябре 2015 г. до 3,8 часа в сентябре 2016 г. И таких примеров десятки, если не сотни.
Система непрерывных улучшений позволила достичь высокого уровня вовлеченности персонала в процесс развития. Сегодня сотрудники завода подают около 2 тыс. предложений по улучшениям в месяц, что в 2017 г. принесло эффект около 200 млн. руб. За последние годы ВМЗ добился существенного повышения качества продукции, что помогло ОМК усилить позиции на российском и мировом рынке сварных труб, в частности, в нефтегазовом сегменте.
Основная работа по непрерывным улучшениям ведется на ВМЗ в МИГах (малые инициативные группы) — такую аббревиатуру, совпадающую с названием известного самолета, придумали на заводе для обозначения японских кружков качества. В начале декабря 2017 г. на предприятии насчитывалось более 310 малых инициативных групп, в работе которых участвует свыше 1,9 тыс. сотрудников. Всего в МИГах реализовано к настоящему времени около 900 проектов, свыше 320 находится в работе. Благодаря их деятельности завод получил прямой финансовый выигрыш более 80 млн. руб., не считая косвенного воздействия.
Д. Махров, директор ВМЗ по качеству, рассказал подробнее, что такое МИГ. Это добровольная группа из 3—9 человек (чаще всего 4—6), работающих на одном производственном участке и решающих какую-либо проблему, непосредственно влияющую на производственные процессы. Группы формируют графики еженедельных встреч, на которых происходит поиск первопричин и вырабатываются мероприятия по их устранению.
На японских предприятиях такие кружки качества — привычный инструмент, существующий десятилетия. На ВМЗ их пришлось создавать с нуля. Первым этапом стало определение лидеров. В чем-то эту задачу решало руководство, подыскивая авторитетных сотрудников, которым поручали определенные задания, потом люди начали сами выдвигаться, проявлять инициативу, раз она поддерживается и поощряется. Из практики первых групп родился стандарт по деятельности МИГов, на который могли опираться новые малые коллективы. Затем лидеров МИГов учили в Академии ПС искать и выявлять проблемы, анализировать, вести мозговой штурм, управлять членами групп.
Рабочие зачастую находили решение достаточно сложных проблем, до которых могли просто не дойти руки у руководства. Например, одна из групп занялась проблемой, возникшей при резке слябов. Два резака работали не совсем соосно, из-за чего слябы приходилось дорабатывать вручную, теряя время и ресурсы. Члены МИГа выявили проблему и привлекли специалистов к ее решению. В результате отремонтировали несколько узлов, на других провели регламентные работы, улучшили программное обеспечение. В результате повысилось качество резки и значительно снизился расход кислорода и природного газа.
Другой случай — в центральной заводской лаборатории дирекции по качеству обратили внимание на высокую долю неудовлетворительных результатов испытаний из-за разрушения образцов. Создали инициативную группу. Проект оказался весьма сложным, этап диагностики и выявления первопричин проблем длился более пяти месяцев. Была сформирована программа мероприятий, в которую вошло в том числе изучение передового опыта других предприятий. Привлекли специалистов для разработки и внедрения новых стандартов отбора образцов, автоматизировали процессы, для того чтобы снизить влияние человеческого фактора, модернизировали оборудование. В итоге процент брака при проведении данных испытаний сократился почти в 8 раз, что значительно превысило изначальное задание.
По словам Д. Махрова, данные случаи показали людям, что они реально могут что-то сделать. Это помогло продвинуть дальше идею с МИГами и повысить уровень вовлеченности персонала. На сегодняшний день участниками малых инициативных группы на предприятии являются около 20% сотрудников, но руководство ВМЗ надеется довести долю до 50%. Чтобы продвинуть идею, на заводе ежеквартально с 2016 г. проводятся конкурсы на лучший проект МИГов с призовым фондом 1,5 млн. руб.
Как отмечает президент ТЕС Тосихиро Ямада, топ-менеджеры компаний часто уделяют основное внимание достижению благоприятных показателей — доходу, прибыли, рентабельности, отношению долга к EBTDA. Однако система бережливого производства, по его словам, помогает оптимизировать использование внутренних ресурсов — персонала, технологий, оборудования, системы организации труда. И, как показывает опыт мирового бизнеса, благодаря высокой эффективности на этих направлениях, личностному развитию сотрудников, стабильно высокому качеству обеспечиваются хорошие финансовые результаты. В целом все участники конференции «Опыт развития эффективных производственных систем в России» отметили очевидные успехи в развитии компаний, выбравших путь внедрения инструментов бережливого производства.
***
ВМЗ стал первой «серебряной» компанией в России. Кстати, освоением системы бережливого производства занимаются в нашей стране уже несколько десятков предприятий, в том числе другие заводы группы ОМК.
Как показали аудиты, проведенные TEC на Выксунском металлургическом заводе, еще в 2015 г. деятельность руководства предприятия получила высокую оценку.
На Выксунском металлургическом заводе создание адаптированной производственной системы, как рассказал управляющий директор предприятия А. Барыков, началось в 2011 г. Оно имело четкие цели — активизация темпов роста и снижение потерь.
Лучшие практики формализуются в виде рабочих стандартов — карт пошагового выполнения операций и стандартных операционных процедур для каждого рабочего места, для каждой операции. Причем составляют эти документы группы сотрудников, в которые входят и сами рабочие, которые, можно сказать, пишут их для себя.
Началом преобразований на заводе стала реализация проектов повышения эффективности производственных участков и функций. С того момента реализовано более 50 проектов с экономическим эффектом
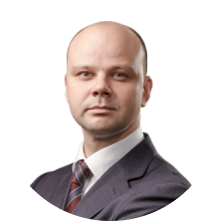
Читайте еще