Владимир Маркин – о сотрудничестве с ПАО «Газпром»
07.04.2017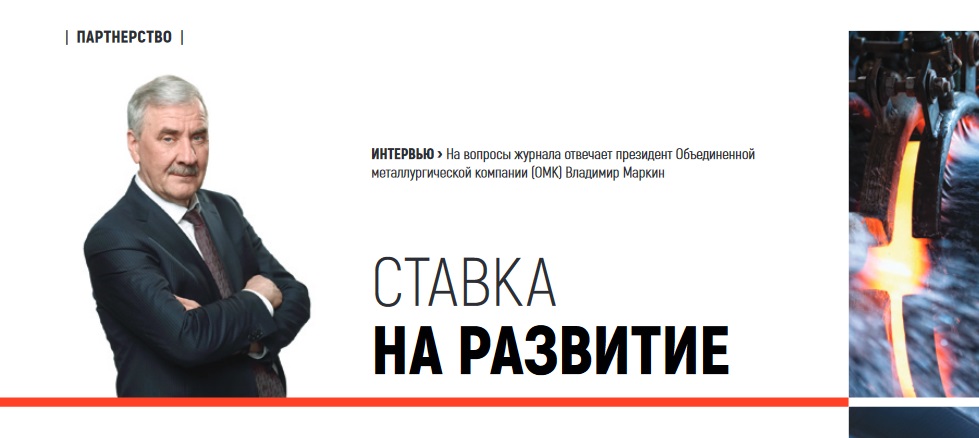
Ставка на развитие
На вопросы журнала «Газпром» отвечает президент Объединенной металлургической компании Владимир Маркин.
Стоп импорту
– Владимир Степанович, ОМК в 2005 году начала выпуск труб большого диаметра для магистральных трубопроводов. Какие решения позволили это сделать?
– В нашей стране исторически не было достаточного количества современных трубных мощностей по большим диаметрам. Сейчас уже это трудно представить, но еще в 2000-х годах наша промышленность не выпускала трубы для магистральных газопроводов. Для их строительства Россия по-прежнему была вынуждена, как в 1970-е, покупать трубы по импорту. Тогда у руководства «Газпрома» возникло стратегическое понимание, что в России нужно создавать собственное производство качественных труб большого диаметра. Это было зафиксировано в программах развития топливно-энергетического комплекса, принятых в отрасли в начале 2000-х были.
В планах «Газпрома» мы видели будущие проекты новых газовых магистралей большой протяженности, которые должны надежно и долгосрочно работать в самых сложных условиях. Для их строительства требовались трубы так называемого русского размера – диаметром 1420 мм. Трубы такого сортамента тогда были готовы предложить только японские и немецкие производители. И в 2003 году компания приняла решение: пора менять ситуацию.
В то время никто не мог дать гарантий, что планируемые проекты будут реализованы. Тем не менее мы приняли решение организовать на Выксунском металлургическом заводе (ВМЗ) комплекс по производству прямошовных одношовных труб диаметром до 1420 мм. Примечательно, что до 2005 проектные рабочие давления магистральных трубопроводов были 5,4 и 7,4 МПа. При этом в зависимости от категории толщина стенки трубы составляла 15,7–18,7 и для самой высокой категории 23 мм.
На внутренних инвесткомитетах мы доказывали, что нам необходимо выпускать трубы, которые могли бы выдерживать давление существенно выше, ведь магистрали могли быть проложены на тысячи километров или проходить по морскому дну. Увеличение толщины стенки выливалось в существенное удорожание инвестпроектов, но мы все-таки заложили такую возможность. И действительно, через несколько лет требования по давлению начали расти, толщина стенок сухопутных газопроводов достигала 32 мм, появилась необходимость в трубах для подводных переходов с толщиной стенки более 40 мм. Так что мы оказались правы, верно спрогнозировав перспективные требования. Это открыло нам возможности участия в новых сложных проектах.
В 2005 году на нашем Выксунском металлургическом заводе в Нижегородской области начал работу первый в стране комплекс по выпуску одношовных прямошовных труб для магистральных трубопроводов «русского размера». И когда появился заказ на трубы для строительства сухопутной части «Северного потока», который открывал новый экспортный маршрут российского газа в Европу, мы смогли начать его выполнение с первых дней запуска комплекса.
Сотрудничество с «Газпромом» в рамках Программы научно-технического сотрудничества дало нам понимание перспективных требований и подготовило наши производства и специалистов к участию в международных газопроводных проектах. Новой проверкой для нас стал морской газопровод «Северный поток». Запомнился такой случай. После проведения инспекции производства в рамах поданной заявки на участие в этом проекте шли собеседования с руководителями международной компании. Нам говорили: у вас есть современное оборудование, квалифицированный персонал, передовые технологии, но справитесь ли вы без серьезного подводного опыта? Мы заверили, что справимся, так как у нас есть опыт участия в проектах «Газпрома». В итоге Nord Stream поверила в нас, и ОМК стала первой и единственной российской трубной компанией, допущенной к участию в этом проекте. Всего для двух ниток газопровода «Северный поток» ОМК отгрузила более 460 тыс. т труб. В рамках контракта была про изведена партия труб с толщиной стенки до 41 мм. Это уникальные трубы, которые выдерживают давление до 22 МПа. Для компрессор ной станции Портовая, которая является начальной точкой «Северного потока», компания произвела партию труб, которые по своим характеристикам способны выдерживать давление до 250 МПа, что не имеет аналогов во всем мире. В 2009 году мы увеличили мощности цеха по выпуску таких труб, доведя их до 900 тыс. т в год.
– А металлические заготовки для труб вы делали сами?
– Для удовлетворения потребностей нам было недостаточно листа (мы частично использовали отечественный, но его основные объемы вынуждены были завозить из-за рубежа). Чтобы не зависеть от его закупок, в 2011 году мы построили в Выксе толстолистовой прокатный металлургический комплекс-стан – 5000 (МКС-5000). Позже для обеспечения его стальной заготовкой было подписано долгосрочное соглашение с Новолипецким металлургическим комбинатом.
Благодаря курсу «Газпрома», направленному на замещение трубного импорта, в Центральной России появился один из самых современных в мире комплексов по производству труб большого диаметра любого уровня сложности, включая трубы 1420х48 мм, и высоких классов стали по прочности. Отмечу, что инвестиции ОМК в развитие производства стали, проката и труб в Выксе составили более 125 млрд рублей. Комплекс обеспечивает работой 15 тыс. сотрудников. Выксунский металлургический завод является вторым по величине налогоплательщиком региона.
Значение решений 2000-х годов и движущую силу «Газпрома» в их принятии трудно переоценить. Сначала мы, а затем и другие трубные компании построили современные мощности, благодаря чему на сегодня мы смогли на 100% заместить импорт в трубах большого диаметра.
– Как участие в проектах «Газпрома» помогает развивать производство новых видов трубной продукции?
– В настоящее время мы работаем с «Газпромом» по Программе научно-технического сотрудничества. Это долгосрочный, большой проект, который предполагает 27 направлений. В рамках данных программ до 2021 года планируется выполнить более 60 инновационных научно-исследовательских, опытно-конструкторских и технологических работ. Особое внимание будет уделено разработке импортозамещающей продукции. Мы с успехом замещаем импорт поставками труб, трубодеталей и трубопроводной арматуры из российской стали. Растет доля отечественного покрытия при производстве труб.
В 2014 году мы осуществили крупную поставку отводов, тройников и трубных узлов для компрессорной станции «Русская», рассчитанных на сверхвысокое давление более чем 28 МПа, что является мировым рекордом. Также из сложных проектов отмечу участие компании в проекте «Турецкий поток». Мы поста вили трубы, которые способны работать на глубине 2,5 км в среде, богатой сероводородом. Такие трубы были впервые выпущены и сертифицированы в нашей стране. С осени прошлого года мы участвуем в поставках для «Северного потока – 2». Предполагаем, что половина труб для этого проекта будет изготовлена из широкого листового проката собственного производства ВМЗ. Это первый международный проект такого высочайшего класса, где будет использоваться полностью отечественная труба из локализованной нами цепочки «от руды до трубы» в сегменте ТБД, включая сляб, лист, саму трубу и антикоррозионные покрытия. Именно эта российская цепочка, по отзывам клиентов, позволяет добиться максимальной стабильности и ритмичности поставок.
Технологический рывок
– Условия добычи и транспортировки углеводородов постоянно усложняются. Готовы ли вы предложить передовые отечественные решения в этой области?
– Готовы и делаем это. В частности, мы освоили производство высокодеформируемых труб, которые могут применяться в сейсмоактивных районах, на участках активных тектонических разломов и в вечномерзлых грунтах. Исследования подтвердили возможности труб сохранять свои эксплуатационные свойства при рабочих температурах до минус 60 градусов. Высокодеформируемые трубы ВМЗ превосходят зарубежные аналоги. Они, например, нужны для ряда участков проекта «Сила Сибири».
Мы готовы полностью обеспечить потребности «Газпрома» в таких трубах. Мы начали выпуск труб большого диаметра и соединительных деталей для трубопроводов «Газпрома» с повышенной устойчивостью к сероводородному растрескиванию. Продукция, отвечающая таким требованиям, уже поставлена для обустройства месторождений Оренбуржья. Также ОМК совместно с «Газпром ВНИИГАЗ» произвела опытную партию труб класса прочности Х100 из собственного листа. Трубы полностью соответствуют техническим требованиям.
– Важный элемент современных газопроводных систем – трубопроводная арматура. Как обстоят дела с ней?
– В трубопроводной арматуре доля локализации также существенная, составляет 70–80%. Но есть области, не охваченные пока импортозамещением. Например, добыча и транспортировка газа российского шельфа, проекты СПГ, а также эксплуатация на месторождениях, которые характеризуются повышенным содержанием агрессивных компонентов, или на компрессорных станциях, где нужны высокие давления. Для того чтобы «Газпрому» не зависеть от импорта трубопроводной арматуры, ОМК создает в России производство ее полной линейки и в нужном количестве. Год назад мы подписали с «Газпромом» долгосрочный договор на обеспечение нужд газовой компании шаровыми кранами для специальных условий эксплуатации. Серьезные области применения – высокие давления, низкие температуры и агрессивные среды – накладывают высочайшие требования к качеству. В стране пока такого уровня технологий в области арматуростроения нет. Но нас это не пугает.
Для реализации соглашения мы начали строить в Челябинске производственный комплекс, не имеющий аналогов в России. Продукция нового предприятия – Уральского завода специального арматуростроения (УЗСА) – это шаровые краны, предназначенные для работы на компрессорных станциях, в среде с повышенным содержанием механических примесей и агрессивных химических компонентов, таких как сероводород, а также в среде сжиженного природного газа при сверхнизких температурах. Первые образцы импортозамещающей продукции мы показали руководителям «Газпрома» и Министерства промышленности и торговли России в октябре 2016 года на VI Петербургском международном газовом форуме и готовы производить все комплектующие самостоятельно или размещать их изготовление на отечественных предприятиях. Уже сейчас мы достигли уровня локализации в 20%. Часть образцов уже прошла испытания или готовится к ним на объектах «Газпрома». Освоение выпуска шаровых кранов для специальных условий по полному циклу запланировано в 2018–2019 годах с максимальным уровнем локализации в последующие несколько лет, чего не может обеспечить больше ни одно арматуростроительное предприятие в России.
– Каковы ближайшие планы?
– Для нас, производителей, большинство проектов «Газпрома» – это технологический и интеллектуальный вызов. Например, оборудование УЗСА будет состоять из комплекса высокоточного металлообрабатывающего, контрольно-измерительного и испытательного оборудования, оборудования для нанесения сверхзвукового газопламенного напыления и других высокотехнологичных процессов, которые сейчас не применяются в отечественном арматуростроении. Кроме высочайших требований по качеству и технологичности, работа с «Газпромом» требует новых идей по экономии средств и времени заказчика. Одной из таких идей стало комплексное предложение.
Наша стратегическая цель – стать поставщиком комплексных решений для газовой и нефтяной отраслей. Развиваем это направление с 2014 года. В частности, для «Газпрома» мы готовы переходить от отдельных поставок труб и трубопроводной арматуры к поставкам комплексных заказов, предлагать для обустройства месторождений наилучшие технические решения заводской сборки – например, блочное оборудование. Не нужно самим собирать блок по частям, работать одновременно с разными производителями. Мы готовы взять это на себя, что позволит значительно сократить затраты заказчика и обеспечит унификацию решений, технической документации.
В блоках используются трубы, детали трубопроводов, трубопроводная арматура. В нашей компании сосредоточено производство основных частей для таких конструкций, что позволяет гарантировать качество и строго соблюдать сроки поставок. Также мы менее зависимы от поставщиков. Блочное оборудование – технически сложный вид продукции, это комплексное инжиниринговое решение. Для его разработки в дополнение к инженерно-технологическому центру в Выксе мы открыли еще один, в Уфе. Блочные и укрупненные решения можно использовать в сложных условиях добычи газа, например, в северных районах. Мы видим развитие производства такого оборудования весьма перспективным.
На вопросы журнала «Газпром» отвечает президент Объединенной металлургической компании Владимир Маркин.
Стоп импорту
– Владимир Степанович, ОМК в 2005 году начала выпуск труб большого диаметра для магистральных трубопроводов. Какие решения позволили это сделать?
– В нашей стране исторически не было достаточного количества современных трубных мощностей по большим диаметрам. Сейчас уже это трудно представить, но еще в 2000-х годах наша промышленность не выпускала трубы для магистральных газопроводов. Для их строительства Россия по-прежнему была вынуждена, как в 1970-е, покупать трубы по импорту. Тогда у руководства «Газпрома» возникло стратегическое понимание, что в России нужно создавать собственное производство качественных труб большого диаметра. Это было зафиксировано в программах развития топливно-энергетического комплекса, принятых в отрасли в начале 2000-х были.
В планах «Газпрома» мы видели будущие проекты новых газовых магистралей большой протяженности, которые должны надежно и долгосрочно работать в самых сложных условиях. Для их строительства требовались трубы так называемого русского размера – диаметром 1420 мм. Трубы такого сортамента тогда были готовы предложить только японские и немецкие производители. И в 2003 году компания приняла решение: пора менять ситуацию.
В то время никто не мог дать гарантий, что планируемые проекты будут реализованы. Тем не менее мы приняли решение организовать на Выксунском металлургическом заводе (ВМЗ) комплекс по производству прямошовных одношовных труб диаметром до 1420 мм. Примечательно, что до 2005 проектные рабочие давления магистральных трубопроводов были 5,4 и 7,4 МПа. При этом в зависимости от категории толщина стенки трубы составляла 15,7–18,7 и для самой высокой категории 23 мм.
На внутренних инвесткомитетах мы доказывали, что нам необходимо выпускать трубы, которые могли бы выдерживать давление существенно выше, ведь магистрали могли быть проложены на тысячи километров или проходить по морскому дну. Увеличение толщины стенки выливалось в существенное удорожание инвестпроектов, но мы все-таки заложили такую возможность. И действительно, через несколько лет требования по давлению начали расти, толщина стенок сухопутных газопроводов достигала 32 мм, появилась необходимость в трубах для подводных переходов с толщиной стенки более 40 мм. Так что мы оказались правы, верно спрогнозировав перспективные требования. Это открыло нам возможности участия в новых сложных проектах.
В 2005 году на нашем Выксунском металлургическом заводе в Нижегородской области начал работу первый в стране комплекс по выпуску одношовных прямошовных труб для магистральных трубопроводов «русского размера». И когда появился заказ на трубы для строительства сухопутной части «Северного потока», который открывал новый экспортный маршрут российского газа в Европу, мы смогли начать его выполнение с первых дней запуска комплекса.
Сотрудничество с «Газпромом» в рамках Программы научно-технического сотрудничества дало нам понимание перспективных требований и подготовило наши производства и специалистов к участию в международных газопроводных проектах. Новой проверкой для нас стал морской газопровод «Северный поток». Запомнился такой случай. После проведения инспекции производства в рамах поданной заявки на участие в этом проекте шли собеседования с руководителями международной компании. Нам говорили: у вас есть современное оборудование, квалифицированный персонал, передовые технологии, но справитесь ли вы без серьезного подводного опыта? Мы заверили, что справимся, так как у нас есть опыт участия в проектах «Газпрома». В итоге Nord Stream поверила в нас, и ОМК стала первой и единственной российской трубной компанией, допущенной к участию в этом проекте. Всего для двух ниток газопровода «Северный поток» ОМК отгрузила более 460 тыс. т труб. В рамках контракта была про изведена партия труб с толщиной стенки до 41 мм. Это уникальные трубы, которые выдерживают давление до 22 МПа. Для компрессор ной станции Портовая, которая является начальной точкой «Северного потока», компания произвела партию труб, которые по своим характеристикам способны выдерживать давление до 250 МПа, что не имеет аналогов во всем мире. В 2009 году мы увеличили мощности цеха по выпуску таких труб, доведя их до 900 тыс. т в год.
– А металлические заготовки для труб вы делали сами?
– Для удовлетворения потребностей нам было недостаточно листа (мы частично использовали отечественный, но его основные объемы вынуждены были завозить из-за рубежа). Чтобы не зависеть от его закупок, в 2011 году мы построили в Выксе толстолистовой прокатный металлургический комплекс-стан – 5000 (МКС-5000). Позже для обеспечения его стальной заготовкой было подписано долгосрочное соглашение с Новолипецким металлургическим комбинатом.
Благодаря курсу «Газпрома», направленному на замещение трубного импорта, в Центральной России появился один из самых современных в мире комплексов по производству труб большого диаметра любого уровня сложности, включая трубы 1420х48 мм, и высоких классов стали по прочности. Отмечу, что инвестиции ОМК в развитие производства стали, проката и труб в Выксе составили более 125 млрд рублей. Комплекс обеспечивает работой 15 тыс. сотрудников. Выксунский металлургический завод является вторым по величине налогоплательщиком региона.
Значение решений 2000-х годов и движущую силу «Газпрома» в их принятии трудно переоценить. Сначала мы, а затем и другие трубные компании построили современные мощности, благодаря чему на сегодня мы смогли на 100% заместить импорт в трубах большого диаметра.
– Как участие в проектах «Газпрома» помогает развивать производство новых видов трубной продукции?
– В настоящее время мы работаем с «Газпромом» по Программе научно-технического сотрудничества. Это долгосрочный, большой проект, который предполагает 27 направлений. В рамках данных программ до 2021 года планируется выполнить более 60 инновационных научно-исследовательских, опытно-конструкторских и технологических работ. Особое внимание будет уделено разработке импортозамещающей продукции. Мы с успехом замещаем импорт поставками труб, трубодеталей и трубопроводной арматуры из российской стали. Растет доля отечественного покрытия при производстве труб.
В 2014 году мы осуществили крупную поставку отводов, тройников и трубных узлов для компрессорной станции «Русская», рассчитанных на сверхвысокое давление более чем 28 МПа, что является мировым рекордом. Также из сложных проектов отмечу участие компании в проекте «Турецкий поток». Мы поста вили трубы, которые способны работать на глубине 2,5 км в среде, богатой сероводородом. Такие трубы были впервые выпущены и сертифицированы в нашей стране. С осени прошлого года мы участвуем в поставках для «Северного потока – 2». Предполагаем, что половина труб для этого проекта будет изготовлена из широкого листового проката собственного производства ВМЗ. Это первый международный проект такого высочайшего класса, где будет использоваться полностью отечественная труба из локализованной нами цепочки «от руды до трубы» в сегменте ТБД, включая сляб, лист, саму трубу и антикоррозионные покрытия. Именно эта российская цепочка, по отзывам клиентов, позволяет добиться максимальной стабильности и ритмичности поставок.
Технологический рывок
– Условия добычи и транспортировки углеводородов постоянно усложняются. Готовы ли вы предложить передовые отечественные решения в этой области?
– Готовы и делаем это. В частности, мы освоили производство высокодеформируемых труб, которые могут применяться в сейсмоактивных районах, на участках активных тектонических разломов и в вечномерзлых грунтах. Исследования подтвердили возможности труб сохранять свои эксплуатационные свойства при рабочих температурах до минус 60 градусов. Высокодеформируемые трубы ВМЗ превосходят зарубежные аналоги. Они, например, нужны для ряда участков проекта «Сила Сибири».
Мы готовы полностью обеспечить потребности «Газпрома» в таких трубах. Мы начали выпуск труб большого диаметра и соединительных деталей для трубопроводов «Газпрома» с повышенной устойчивостью к сероводородному растрескиванию. Продукция, отвечающая таким требованиям, уже поставлена для обустройства месторождений Оренбуржья. Также ОМК совместно с «Газпром ВНИИГАЗ» произвела опытную партию труб класса прочности Х100 из собственного листа. Трубы полностью соответствуют техническим требованиям.
– Важный элемент современных газопроводных систем – трубопроводная арматура. Как обстоят дела с ней?
– В трубопроводной арматуре доля локализации также существенная, составляет 70–80%. Но есть области, не охваченные пока импортозамещением. Например, добыча и транспортировка газа российского шельфа, проекты СПГ, а также эксплуатация на месторождениях, которые характеризуются повышенным содержанием агрессивных компонентов, или на компрессорных станциях, где нужны высокие давления. Для того чтобы «Газпрому» не зависеть от импорта трубопроводной арматуры, ОМК создает в России производство ее полной линейки и в нужном количестве. Год назад мы подписали с «Газпромом» долгосрочный договор на обеспечение нужд газовой компании шаровыми кранами для специальных условий эксплуатации. Серьезные области применения – высокие давления, низкие температуры и агрессивные среды – накладывают высочайшие требования к качеству. В стране пока такого уровня технологий в области арматуростроения нет. Но нас это не пугает.
Для реализации соглашения мы начали строить в Челябинске производственный комплекс, не имеющий аналогов в России. Продукция нового предприятия – Уральского завода специального арматуростроения (УЗСА) – это шаровые краны, предназначенные для работы на компрессорных станциях, в среде с повышенным содержанием механических примесей и агрессивных химических компонентов, таких как сероводород, а также в среде сжиженного природного газа при сверхнизких температурах. Первые образцы импортозамещающей продукции мы показали руководителям «Газпрома» и Министерства промышленности и торговли России в октябре 2016 года на VI Петербургском международном газовом форуме и готовы производить все комплектующие самостоятельно или размещать их изготовление на отечественных предприятиях. Уже сейчас мы достигли уровня локализации в 20%. Часть образцов уже прошла испытания или готовится к ним на объектах «Газпрома». Освоение выпуска шаровых кранов для специальных условий по полному циклу запланировано в 2018–2019 годах с максимальным уровнем локализации в последующие несколько лет, чего не может обеспечить больше ни одно арматуростроительное предприятие в России.
– Каковы ближайшие планы?
– Для нас, производителей, большинство проектов «Газпрома» – это технологический и интеллектуальный вызов. Например, оборудование УЗСА будет состоять из комплекса высокоточного металлообрабатывающего, контрольно-измерительного и испытательного оборудования, оборудования для нанесения сверхзвукового газопламенного напыления и других высокотехнологичных процессов, которые сейчас не применяются в отечественном арматуростроении. Кроме высочайших требований по качеству и технологичности, работа с «Газпромом» требует новых идей по экономии средств и времени заказчика. Одной из таких идей стало комплексное предложение.
Наша стратегическая цель – стать поставщиком комплексных решений для газовой и нефтяной отраслей. Развиваем это направление с 2014 года. В частности, для «Газпрома» мы готовы переходить от отдельных поставок труб и трубопроводной арматуры к поставкам комплексных заказов, предлагать для обустройства месторождений наилучшие технические решения заводской сборки – например, блочное оборудование. Не нужно самим собирать блок по частям, работать одновременно с разными производителями. Мы готовы взять это на себя, что позволит значительно сократить затраты заказчика и обеспечит унификацию решений, технической документации.
В блоках используются трубы, детали трубопроводов, трубопроводная арматура. В нашей компании сосредоточено производство основных частей для таких конструкций, что позволяет гарантировать качество и строго соблюдать сроки поставок. Также мы менее зависимы от поставщиков. Блочное оборудование – технически сложный вид продукции, это комплексное инжиниринговое решение. Для его разработки в дополнение к инженерно-технологическому центру в Выксе мы открыли еще один, в Уфе. Блочные и укрупненные решения можно использовать в сложных условиях добычи газа, например, в северных районах. Мы видим развитие производства такого оборудования весьма перспективным.
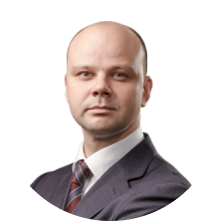
Читайте еще